90L100KA1NN60S3S1E03GBA262626 piston pump
90L100KA1NN60S3S1E03GBA262626 piston pump
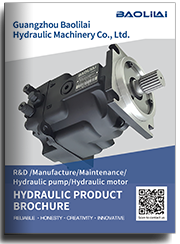
- Product Details
- Applicable Scene
Injection molding is a widely used manufacturing process that shapes a variety of materials into complex forms. The precision of this process is heavily reliant on the equipment and technologies employed, with piston pumps playing a critical role. Piston pumps, known for their ability to deliver consistent pressure and flow rates, are integral to achieving high-precision results in injection molding applications. This article explores how piston pumps contribute to enhanced precision and efficiency in the injection molding process.
90L100-KA-1-NN-60-S-3-S1-E-03-GBA-26-26-26
90L100KA1NN60S3S1E03GBA262626
One of the primary advantages of piston pumps is their ability to provide a uniform flow of hydraulic fluid. Unlike gear or diaphragm pumps, which may experience fluctuations in flow and pressure, piston pumps deliver a steady stream thanks to their design and operational mechanics. This consistent pressure is essential when injecting molten plastic into molds, as variations can lead to defects such as incomplete filling, misalignment, or surface imperfections. A smooth and predictable flow creates a better foundation for achieving the desired dimensions and surface qualities of the molded parts.
83024824
Additionally, piston pumps are capable of generating high pressure, an essential factor in the injection molding process. The ability to exert significant pressure is crucial for ensuring that the molten material fills every nook and cranny of the mold cavity. This is particularly important when dealing with intricate designs or thin-walled components. High-pressure delivery from piston pumps also allows for faster cycle times, enhancing overall productivity without compromising quality.
Piston pumps further support precision in injection molding through their adaptability and control features. Many modern piston pumps are equipped with advanced controls that allow operators to fine-tune pressure settings and monitor flow rates in real-time. This level of control enables manufacturers to adjust the molding process dynamically, responding to changes in material behavior, temperature variations, or mold characteristics. Such adaptability can significantly reduce the margin for error, resulting in higher consistency and product quality.
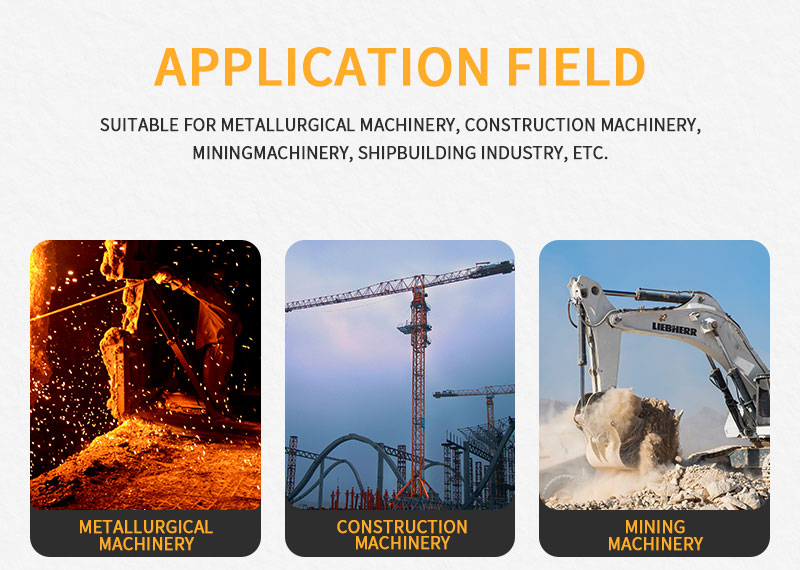
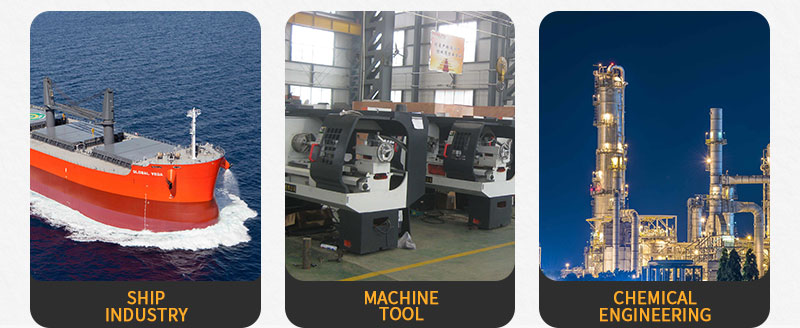