FRL090CLS2220NNN3S1B2A1NNNNNNNNNN high pressure pump
FRL090CLS2220NNN3S1B2A1NNNNNNNNNN high pressure pump
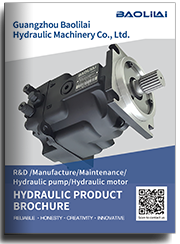
- Product Details
- Applicable Scene
Waterjet cutting technology has revolutionized the manufacturing and construction industries, providing a versatile and efficient method for cutting a wide range of materials. The heart of this process is the high-pressure pump, which generates the water pressure necessary for effective cutting. As industries continue to evolve, so too does the technology behind waterjet cutting, leading to significant innovations in high-pressure pump design and functionality.
FR-L-090C-LS-22-20-NN-N-3-S1B2-A1N-NNN-NNN-NNN
FRL090CLS2220NNN3S1B2A1NNNNNNNNNN
One of the most remarkable advancements in high-pressure pump technology is the development of ultra-high-pressure pumps capable of reaching pressures upwards of 90,000 PSI (pounds per square inch). These pumps enable waterjet cutting systems to deliver a more focused and powerful stream of water, enhancing cutting speed and precision. With increased pressure, operators can cut through thicker and harder materials, such as metals and composites, which were previously challenging to process with standard waterjet systems.
83034840
In addition to pressure enhancements, the integration of advanced materials and engineering techniques in pump design has improved durability and performance. Traditional pumps often utilized metal components, which could wear down over time due to the high-stress conditions experienced during operation. However, the adoption of composite materials and ceramics for critical pump components has led to significant reductions in wear and tear. These innovations not only extend the lifespan of the pumps but also contribute to lower maintenance costs and decreased downtime for waterjet cutting systems.
Another crucial area of development is the efficiency of high-pressure pumps. Modern pump designs incorporate sophisticated electronic controls and variable speed drives that optimize water flow and pressure depending on the cutting requirements. Such systems not only enhance energy efficiency but also allow for greater adaptability during cuts, enabling operators to fine-tune the pressure and speed on-the-fly. This responsiveness can result in improved edge quality and reduced kerf, minimizing material waste and maximizing productivity.
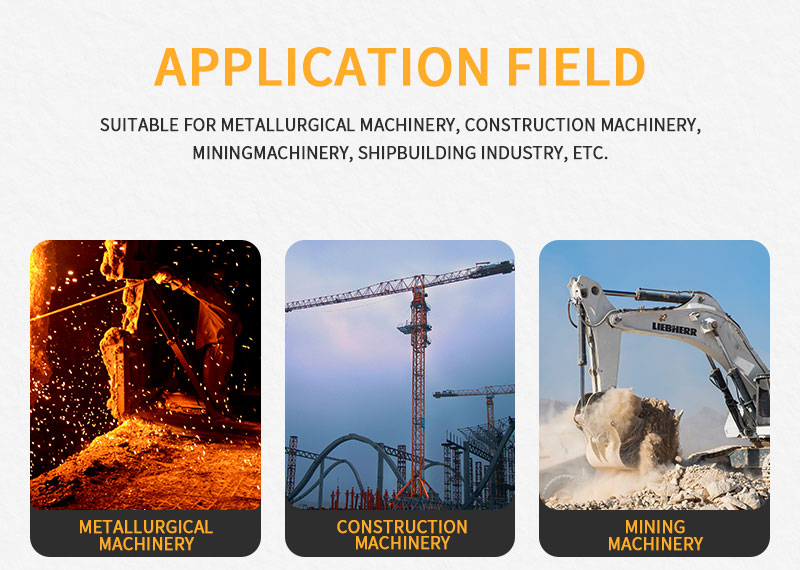
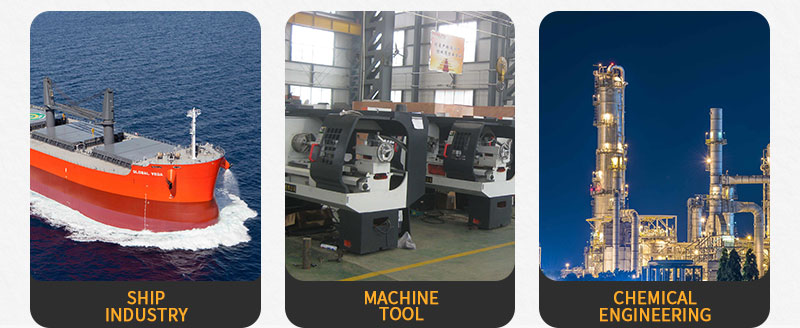