90M100NC0N8N0F1W00NNN0000A0 hydraulic motor
90M100NC0N8N0F1W00NNN0000A0 hydraulic motor
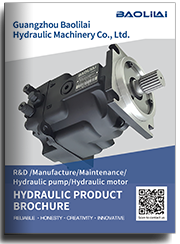
- Product Details
- Applicable Scene
In recent years, the automotive and aerospace industries have increasingly turned to composite materials as a means to enhance performance and efficiency. Composite materials, which are made from two or more constituent materials with significantly different physical or chemical properties, offer distinct advantages over traditional materials. This article examines how the integration of composite materials into piston engines influences performance through weight reduction, thermal management, and overall efficiency.
90-M-100-NC-0-N-8-N-0-F1-W-00-NNN-00-00-A0
90M100NC0N8N0F1W00NNN0000A0
One of the most significant benefits of composite materials is their potential for weight reduction. Traditional piston engine components, such as engine blocks, pistons, and crankshafts, are typically constructed from heavy metals like cast iron and aluminum alloys. By replacing these components with lighter composite alternatives, manufacturers can significantly reduce the overall weight of the engine. This reduction results in a lower vehicle weight, which translates into improved fuel efficiency and enhanced acceleration performance. Furthermore, lighter engines can contribute to better handling and responsiveness in vehicles, leading to an overall improved driving experience.
83012669
Thermal management is another critical area where composite materials can impact piston engine performance. Composite materials often exhibit superior thermal insulation properties compared to traditional metals. This characteristic can help maintain optimal operating temperatures, preventing engine overheating and enhancing reliability. Additionally, composites can be designed to withstand cyclic thermal loads, which is essential for maintaining structural integrity under the harsh conditions experienced in piston engines. With better thermal management, engines can operate more efficiently, leading to reduced emissions and longer service intervals.
The use of composite materials also provides opportunities for improved design flexibility. Engineers can create complex shapes and forms with composites that are difficult or impossible to achieve with metals. This design flexibility allows for the optimization of airflow within the engine, enhancing combustion efficiency. Components can be manufactured in a way that minimizes turbulence and maximizes the air-fuel mixture quality, leading to better combustion performance and increased power output.
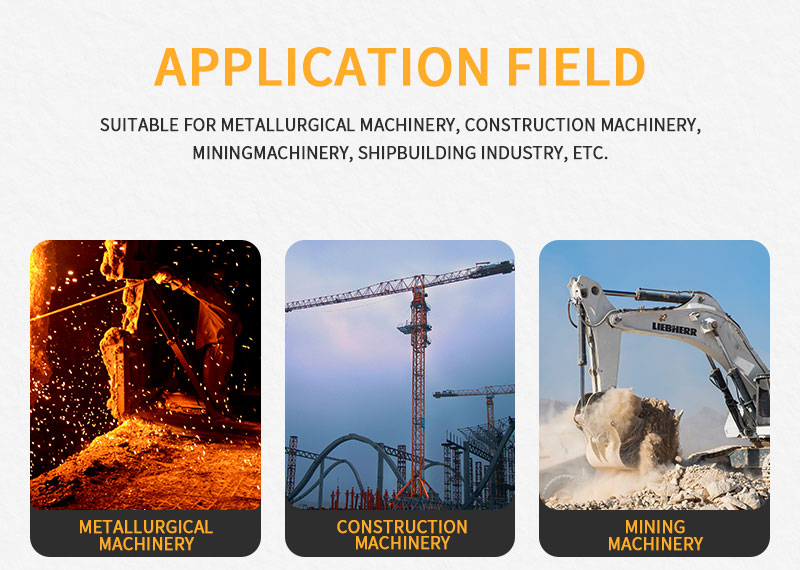
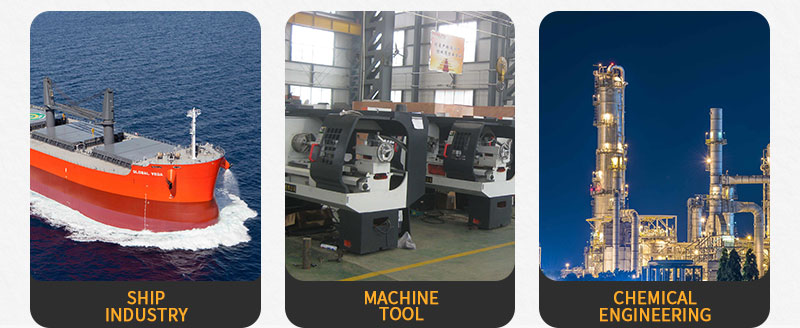