KRL045DLS1820NNN3C2NKA6NKNBNNNNNN high pressure pump
KRL045DLS1820NNN3C2NKA6NKNBNNNNNN high pressure pump
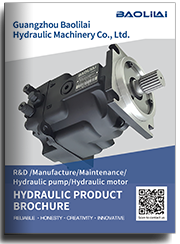
- Product Details
- Applicable Scene
Hydraulic pumps are crucial components in many industrial applications, with Sauer Danfoss hydraulic pumps being widely recognized for their efficiency and reliability. However, even the best equipment can face challenges, particularly when it comes to contaminant infiltration. Foreign particles, water, and debris can compromise the performance and longevity of hydraulic systems. Therefore, it is essential to address this issue proactively. Here are some effective strategies to mitigate contaminant infiltration in Sauer Danfoss hydraulic pumps.
KR-L-045D-LS-18-20-NN-N-3-C2NK-A6N-KNB-NNN-NNN
KRL045DLS1820NNN3C2NKA6NKNBNNNNNN
First and foremost, regular maintenance is critical. Scheduled inspections can help detect signs of wear or potential contamination before they lead to significant problems. During these inspections, it is essential to check for leaks, cracks, and the condition of seals and filters. By keeping the hydraulic system in good condition, it is possible to greatly reduce the risk of contaminants entering the pump.
83004456
In addition to routine maintenance, the implementation of effective filtration systems is paramount. High-quality filters can capture particulates that would otherwise enter the hydraulic fluid and the pump. Consider investing in filtration systems specifically designed for hydraulic applications, which can handle the demands of your equipment. Regularly replacing filters as part of maintenance schedules can further ensure that contaminants are kept at bay.
Another important measure is to ensure proper fluid management. This includes the selection of the right hydraulic fluids and regular monitoring of fluid conditions. Contaminants can often be introduced through poor-quality fluids or by reusing fluids without proper cleaning. Establishing protocols for fluid storage, transfer, and disposal can minimize the risk of contamination.
Environmental control should also be a priority. The areas around the hydraulic systems should be kept clean and free of unnecessary debris. Installing barriers or mats in work areas can help minimize the amount of dirt and contaminants that can come into contact with the hydraulic equipment. Additionally, using closed or sealed systems wherever possible can significantly reduce the risk of infiltrations.
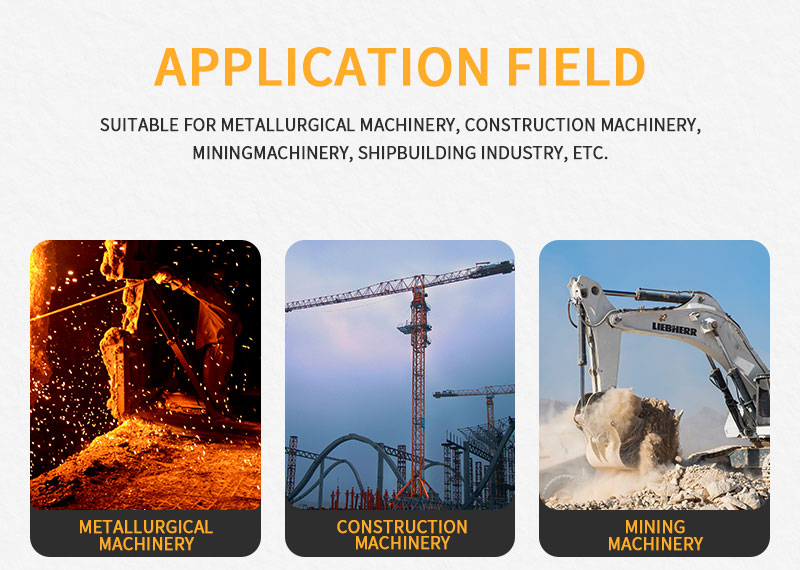
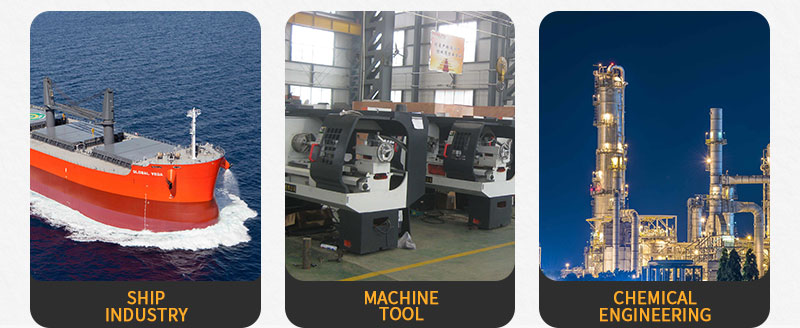