KRR045DLS1620NNK3C2NFA6NPLBNNNNNN sauer danfoss pump
KRR045DLS1620NNK3C2NFA6NPLBNNNNNN sauer danfoss pump
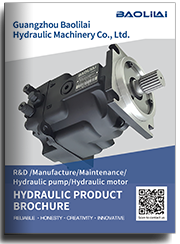
- Product Details
- Applicable Scene
In recent years, the manufacturing landscape has evolved significantly, with automation systems becoming a cornerstone of modern production. Among various components that facilitate automation, hydraulic oil pumps play a critical role. These pumps are essential for powering hydraulic systems that operate machinery, enabling efficient and precise automation processes. This article delves into the design considerations for hydraulic oil pumps tailored for automation systems in factories.
KR-R-045D-LS-16-20-NN-K-3-C2NF-A6N-PLB-NNN-NNN
KRR045DLS1620NNK3C2NFA6NPLBNNNNNN
The first step in designing hydraulic oil pumps for automation systems involves understanding the unique requirements of the application. Different manufacturing processes demand different types of hydraulic systems, influenced by factors such as the nature of the operation, the load to be moved, and the environmental conditions. For instance, a manufacturing plant that requires rapid movement of heavy objects will necessitate a high-performance pump, while lighter operations may benefit from a more compact and energy-efficient design.
83057575
One of the primary considerations in the design of hydraulic oil pumps is the choice of the pump type. Hydraulic pumps can be classified into several categories, including gear pumps, vane pumps, and piston pumps. Each type has its advantages and limitations. Gear pumps, known for their simplicity and robustness, are ideal for applications requiring steady flow and lower pressure. In contrast, piston pumps can provide higher pressures and are suitable for precision applications, making them preferable for sensitive automation tasks.
Another crucial aspect of design is the efficiency of the hydraulic oil pump. With rising energy costs and increasing environmental regulations, optimizing pump efficiency has become imperative. Integrating variable displacement mechanisms can allow the pump to adjust its output based on demand, resulting in significant energy savings. Moreover, using advanced materials and coatings can reduce friction and wear, further enhancing the efficiency and lifespan of the pump.
Temperature management is another critical consideration in hydraulic pump design. Hydraulic systems can generate substantial heat, affecting both performance and reliability. It is essential to incorporate effective cooling systems and thermal management strategies within the pump design to maintain optimal operating temperatures. This may involve integrating oil coolers or designing the pump casing to facilitate heat dissipation.
The hydraulic oil’s properties are also pivotal when designing the pump. Selecting the appropriate hydraulic fluid can enhance the performance and reliability of the system. Factors like viscosity, temperature range, and additives should be carefully evaluated to ensure compatibility with the pump materials and the application requirements. The design must also account for potential leakage and contamination, which can lead to pump failure and increased maintenance costs.
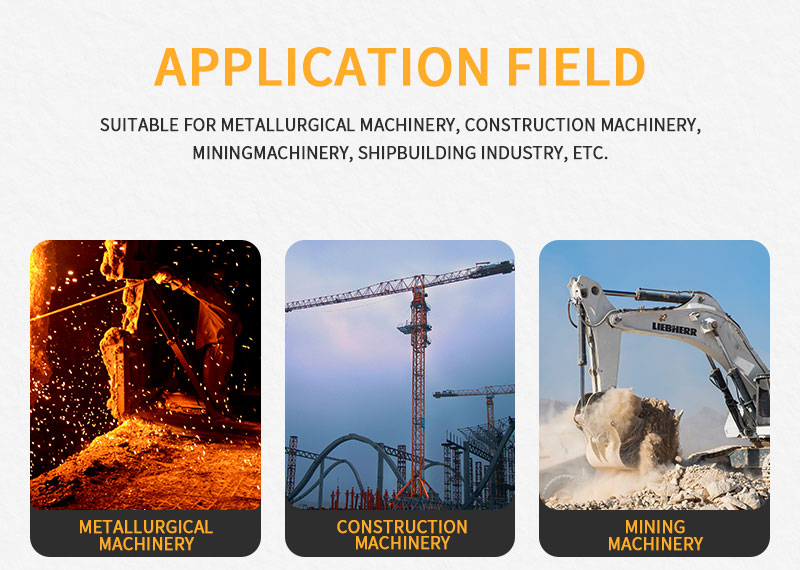
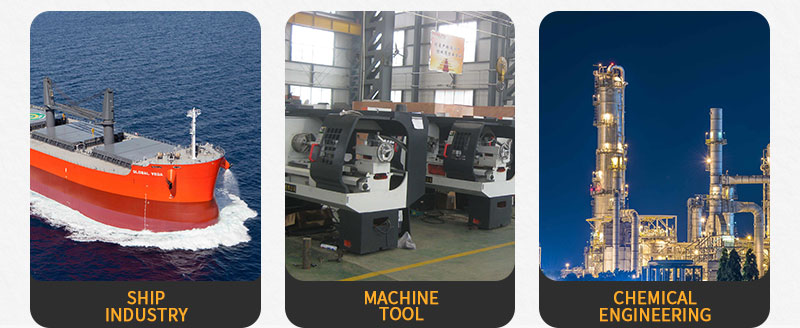