KRR045DPC13NNNNN3C2NFA6NPLBNNNNNN hydraulic pump
KRR045DPC13NNNNN3C2NFA6NPLBNNNNNN hydraulic pump
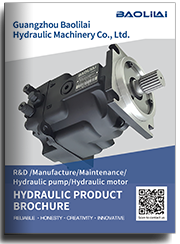
- Product Details
- Applicable Scene
The development of hydraulic systems in aircraft and spacecraft is essential for ensuring reliable performance and operational efficiency. At the heart of these systems are hydraulic oil pumps, which play a crucial role in powering various mechanical components, such as actuators, landing gear, and control surfaces. The design of hydraulic oil pumps for aerospace applications requires a comprehensive understanding of the unique demands and challenges posed by the operating environment.
KR-R-045D-PC-13-NN-NN-N-3-C2NF-A6N-PLB-NNN-NNN
KRR045DPC13NNNNN3C2NFA6NPLBNNNNNN
One of the primary considerations in the design of hydraulic oil pumps for aircraft and spacecraft is weight reduction. Air and space vehicles operate under strict weight constraints, as any additional mass can adversely affect performance and fuel efficiency. Consequently, engineers must prioritize lightweight materials and innovative designs that do not compromise strength and durability. Advanced materials such as carbon fiber composites and aluminum alloys are often utilized to achieve these weight reductions while maintaining structural integrity.
7004304
Another critical factor is the operating environment. Hydraulic systems in aerospace applications must withstand extreme temperature fluctuations, varying pressures, and exposure to contamination. The design of hydraulic oil pumps must ensure reliable operation under these conditions. To achieve this, engineers often employ specialized seals and coatings to prevent leaks and protect against corrosion. Additionally, comprehensive testing must be conducted to ensure that the pump can function optimally within the defined operational limits.
Efficiency is paramount in the design of hydraulic oil pumps for aircraft and spacecraft. High efficiency reduces the energy requirements for the hydraulic system, thereby conserving fuel or electrical power. To enhance efficiency, designers may use advanced hydraulic circuit designs and variable displacement pumps that adjust output flow according to demand. This adaptability not only improves efficiency but also minimizes the risk of overloading other system components.
Safety and reliability are paramount in aerospace applications. Hydraulic systems must perform flawlessly to ensure the safety of passengers and crew, particularly in critical phases such as takeoff and landing. To ensure reliability, a rigorous design qualification process is implemented, which includes finite element analysis (FEA), computational fluid dynamics (CFD), and extensive testing under simulated flight conditions. Designers must also consider redundancy in their systems; for instance, employing dual-pump systems can provide backup functionality in the event of a failure.
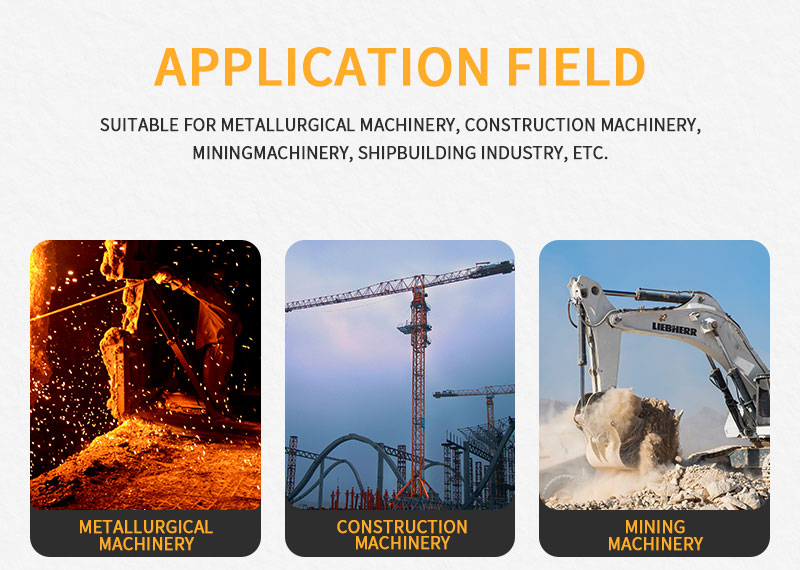
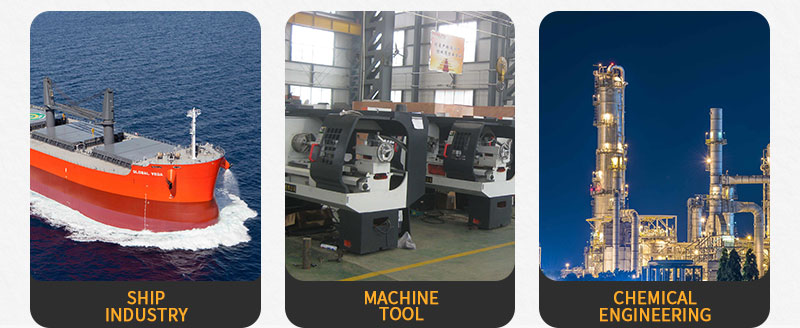