KRR045DLS1320NNN3C3AKA6NKNBNNNNNN sauer danfoss pump
KRR045DLS1320NNN3C3AKA6NKNBNNNNNN sauer danfoss pump
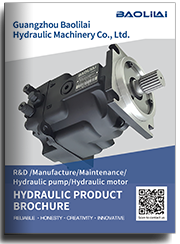
- Product Details
- Applicable Scene
The aviation industry has long recognized the critical importance of reliable hydraulic systems for the safe operation of aircraft. Hydraulic oil pumps are central to these systems, providing the necessary force for various aircraft functions such as flight control surfaces, landing gear, and braking systems. In the context of emergency power systems, the design of these pumps takes on heightened significance, necessitating a focus on redundancy and reliability.
KR-R-045D-LS-13-20-NN-N-3-C3AK-A6N-KNB-NNN-NNN
KRR045DLS1320NNN3C3AKA6NKNBNNNNNN
At the heart of an aircraft’s emergency power system lies the need for immediate and dependable hydraulic assistance in case of primary system failure. Typically, hydraulic systems operate under high pressure, which means that the design of hydraulic oil pumps must not only facilitate consistent performance but also handle extreme conditions. A robust design ensures that, in the event of a malfunction in the primary hydraulic circuit, the backup systems can maintain critical avionics and flight control functionality.
83036553
One fundamental approach to achieving redundancy in hydraulic oil pumps is through the implementation of dual-pump systems. Such systems can employ either parallel or series configurations, providing an additional layer of safety. In parallel configurations, two pumps work simultaneously, allowing for continued operation even if one pump fails. Meanwhile, series configurations may involve one pump serving as a backup to another, automatically activating if the primary pump experiences issues.
Choosing the right materials and components for hydraulic oil pumps is another essential aspect of the design process. Given the exposure to high temperatures and pressures, using materials that can withstand these conditions while minimizing the risk of leakage or failure is critical. Advanced composites and heat-resistant alloys are often utilized to enhance the durability and performance of hydraulic systems.
Moreover, precision engineering plays a significant role in hydraulic pump design. Tolerances must be exceedingly tight to ensure efficiency and performance under varying operational conditions. The use of advanced simulation technologies during the design phase can help to identify potential failure points and optimize pump performance before physical prototypes are built.
Maintenance and accessibility are also crucial considerations in the design of hydraulic oil pumps for emergency power systems. Every component must be easily accessible for regular inspections and repairs to guarantee functionality in emergency scenarios. Designing for maintenance can reduce downtime and ensure that all safety protocols are followed during aircraft servicing.
Training operators and maintenance personnel on the importance of hydraulic system integrity and how to monitor pump performance is vital. Understanding the signs of potential failure and implementing preventive maintenance strategies can significantly reduce the risks associated with hydraulic pump malfunctions.
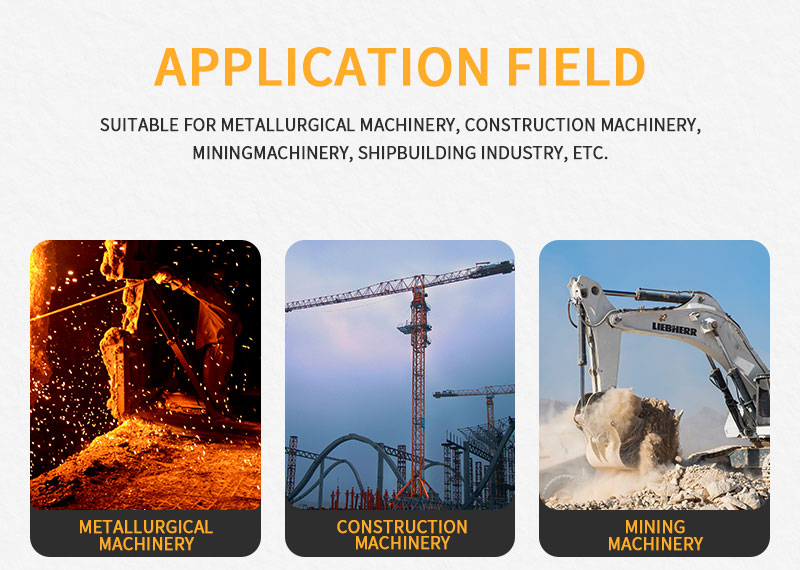
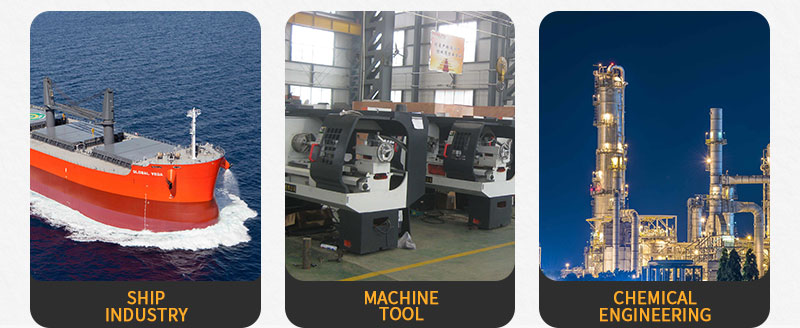