ERR100BBS3120NNE3S1NPA1NAAANNNNNN danfoss pump
ERR100BBS3120NNE3S1NPA1NAAANNNNNN danfoss pump
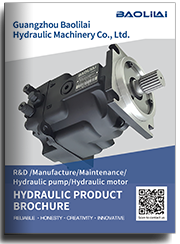
- Product Details
- Applicable Scene
Hydraulic pumps are crucial components in various industrial applications, and their performance directly influences system efficiency and operational costs. In variable-speed systems, the ability to adjust pump performance to meet fluctuating demands presents challenges, particularly performance losses. Addressing these losses is critical for maintaining efficiency, reducing energy consumption, and ensuring reliable operation. Here are several strategies to troubleshoot and solve hydraulic pump performance loss in variable-speed systems.
ER-R-100B-BS-31-20-NN-E-3-S1NP-A1N-AAA-NNN-NNN
ERR100BBS3120NNE3S1NPA1NAAANNNNNN
Identify the Source of Performance Loss
83028433
First, it’s essential to understand the potential causes of performance loss in hydraulic pumps. Common issues include:
Cavitation: This phenomenon occurs when the pressure in the pump drops below the vapor pressure of the hydraulic fluid, leading to the formation of vapor bubbles that collapse and cause damage to pump components. Visual signs include noise and vibration.
Aeration: Introduced air can reduce the pump’s efficiency and cause instability in performance. This often happens due to leaks in the system or low fluid levels.
Worn or Damaged Components: Over time, components such as gears, seals, and actuators can wear down or sustain damage, leading to decreased effectiveness.
Inadequate Fluid Quality: The properties of the hydraulic fluid can significantly impact pump performance. Contaminated, degraded, or the wrong type of fluid can lead to increased wear and reduced efficiency.
System Design Flaws: Inefficient system design, such as incorrect sizing of pumps or pipes, can lead to performance issues, especially in variable-speed applications where load conditions frequently change.
Implement Regular Maintenance
Regular maintenance is key to preventing and addressing performance losses. This includes:
Routine Inspections: Conduct visual checks for leaks, wear, or irregular sounds during operation. Early detection of issues can prevent more extensive damage.
Fluid Analysis: Regularly test the hydraulic fluid for contamination, viscosity, and other characteristics to ensure it meets the required specifications for effective operation.
Component Replacement: Schedule replacement for worn parts and components based on performance data and monitoring.
Utilize Advanced Control Systems
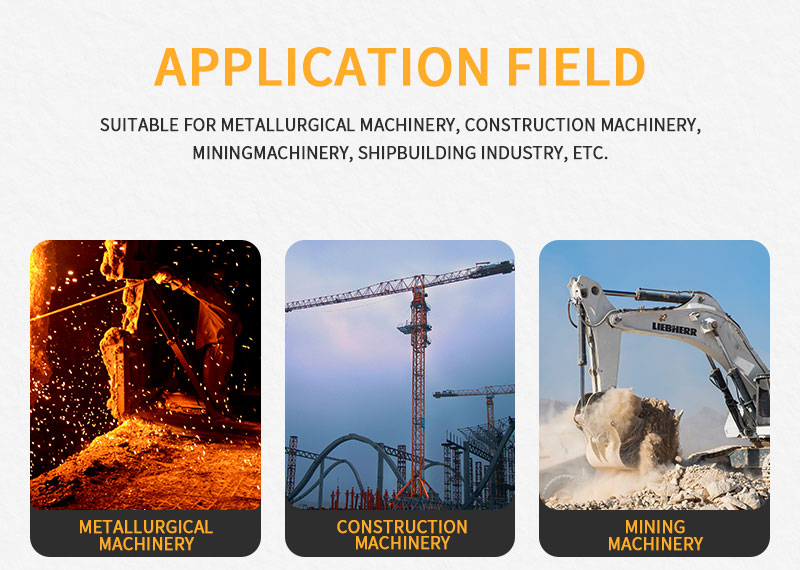
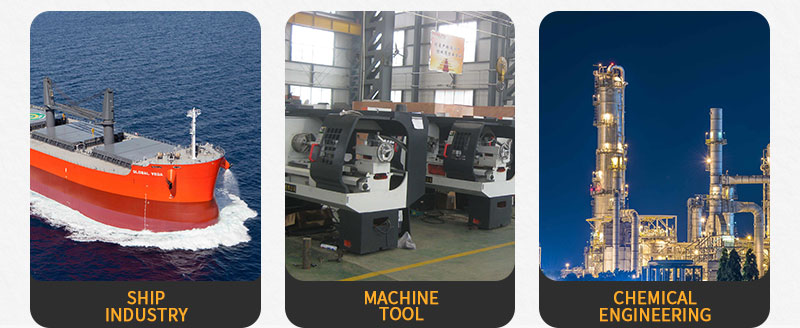