FRR090CRP1610NNN3S1N4A1NNNNNNNNNN high pressure pump
FRR090CRP1610NNN3S1N4A1NNNNNNNNNN high pressure pump
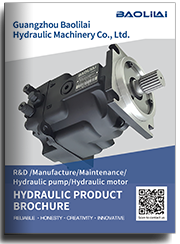
- Product Details
- Applicable Scene
The advancement of technology in the industrial sector has paved the way for innovative solutions aimed at enhancing efficiency, performance, and reliability. One such breakthrough is the implementation of digital twin technology, which holds significant promise for the hydraulic pump industry, particularly within companies like Sauer Danfoss. This article explores the implications and benefits of adopting digital twin technology in the context of Sauer Danfoss hydraulic pumps.
FR-R-090C-RP-16-10-NN-N-3-S1N4-A1N-NNN-NNN-NNN
FRR090CRP1610NNN3S1N4A1NNNNNNNNNN
Digital twin technology refers to the virtual representation of physical assets, processes, or systems, allowing for real-time simulation, analysis, and optimization. By creating a digital replica of hydraulic pumps, Sauer Danfoss can monitor performance, predict failures, and optimize maintenance schedules. This greatly improves the pump’s operational efficiency and lifespan, reducing downtime and maintenance costs.
83037300
One of the primary benefits of digital twin technology in hydraulic pumps is enhanced data collection and analysis. By integrating sensors and IoT devices, real-time data can be captured and fed into the digital twin. This data enables detailed analysis of operational parameters, such as pressure, flow rate, and temperature, which can be used to identify patterns and anomalies. As a result, engineers can make informed decisions, leading to improved design and performance enhancements.
Predictive maintenance is another crucial advantage offered by digital twins. By leveraging predictive analytics, Sauer Danfoss can foresee potential equipment failures before they occur. This proactive approach to maintenance not only minimizes unplanned downtimes but also optimizes the maintenance schedule, ensuring that the pumps remain operational when needed most. The ability to predict when a pump may fail allows for timely interventions, significantly enhancing the productivity of hydraulic systems.
Furthermore, digital twins facilitate the testing and validation of new designs and modifications in a virtual environment. Engineers at Sauer Danfoss can simulate various operating conditions and stress tests without the risk associated with physical prototypes. This accelerates the innovation process, as modifications can be tested and refined before implementation, ensuring optimal performance in the field.
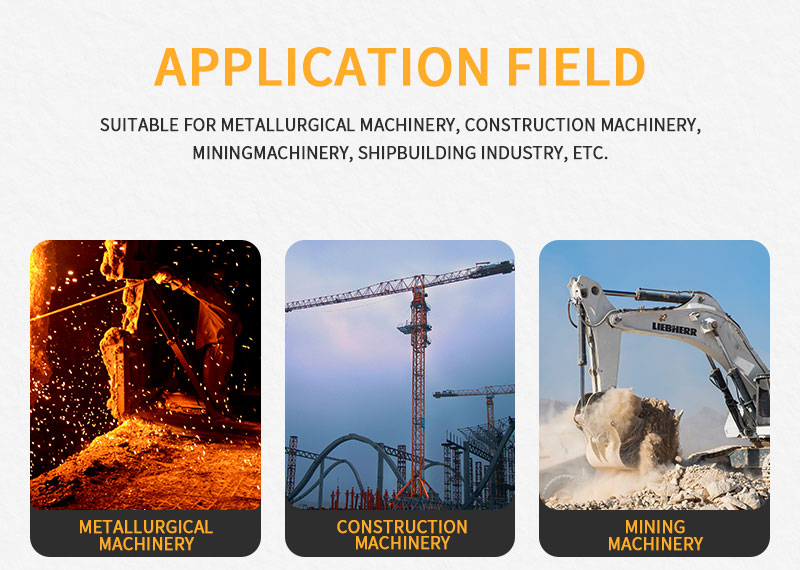
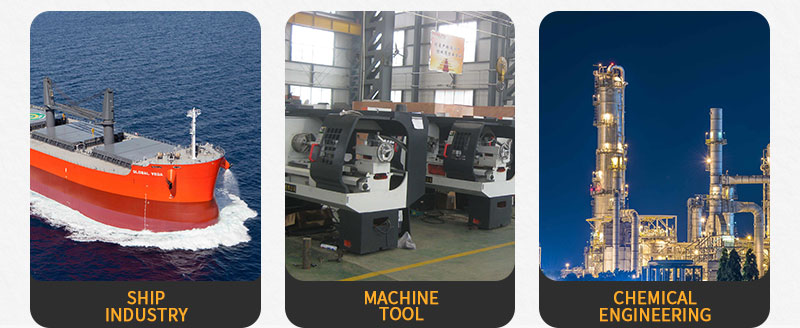