KRR045DLS2125NNN3C2NFA6NPLBNNNNNN high pressure pump
KRR045DLS2125NNN3C2NFA6NPLBNNNNNN high pressure pump
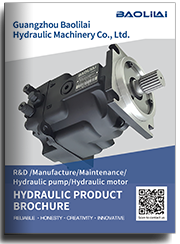
- Product Details
- Applicable Scene
The aerospace industry continually seeks improvements in efficiency, reliability, and performance, particularly in testing environments where precision is paramount. One crucial component that plays a vital role in achieving these objectives is the hydraulic oil pump, especially when used in hydraulic actuators. Hydraulic actuators are essential in various aircraft systems, including flight control surfaces, landing gear, and engine controls. This article explores the key considerations in designing hydraulic oil pumps for hydraulic actuators in the context of aircraft testing.
KR-R-045D-LS-21-25-NN-N-3-C2NF-A6N-PLB-NNN-NNN
KRR045DLS2125NNN3C2NFA6NPLBNNNNNN
Hydraulic systems leverage the incompressibility of hydraulic fluids to transmit power, making them ideal for high-load applications within aircraft. Hydraulic oil pumps serve as the heart of these systems, responsible for generating the hydraulic pressure necessary to operate actuators. Therefore, the design of hydraulic oil pumps must focus on several critical aspects, including pressure requirements, flow rates, efficiency, and integration with the overall hydraulic system.
7004208S
One of the first considerations in hydraulic pump design for actuators is the pressure requirements. Different hydraulic actuators operate under varying pressure conditions, which means that pumps must be designed to generate sufficient pressure to meet these demands. For aircraft testing, where scenarios may simulate extreme operational conditions, pumps should be capable of handling peak pressures while maintaining stable performance.
Flow rate is another significant factor. Hydraulic actuators require a specific flow rate to achieve desired movement speed and responsiveness. The pump must be capable of providing the required flow rate across the entire operational envelope. This typically entails designing pumps with variable displacement capabilities or using pressure-compensated pumps that can adjust output based on system needs.
Efficiency is paramount in aircraft testing to reduce energy consumption and minimize heat generation within the hydraulic system. High-efficiency designs will not only improve overall system performance but also extend the lifespan of hydraulic components. Engineers must carefully select materials and optimize the design to reduce hydraulic losses due to friction and turbulence within the pump.
Integration with the overall hydraulic system is also critical. The design must account for the placement of the pump within the system, piping layout, and the compatibility of hydraulic fluids. Additionally, considerations for heat exchangers and filtration systems are vital to ensure that the hydraulic fluid remains at optimal temperatures and is free from contaminants, thereby maintaining the system’s reliability.
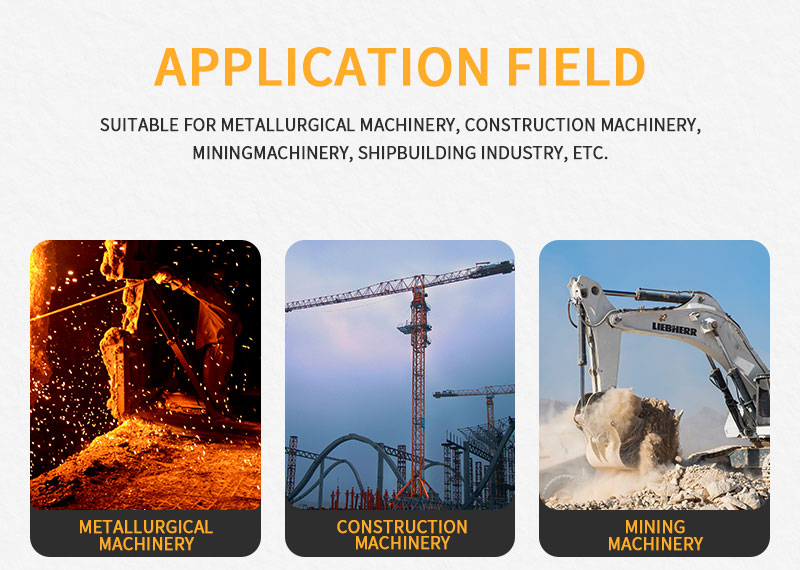
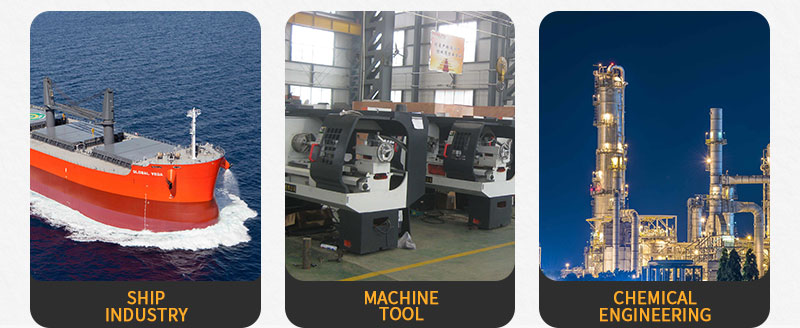