KRR045DLS2014NNN3K2AGA6NAAANNNNNN sauer danfoss pump
KRR045DLS2014NNN3K2AGA6NAAANNNNNN sauer danfoss pump
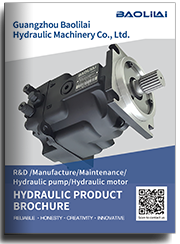
- Product Details
- Applicable Scene
In the modern petrochemical industry, the efficient management of fluids is paramount to operational success. Hydraulic oil pumps play a critical role in fluid control, ensuring precise delivery and pressure regulation of hydraulic fluids across various processes. Designing these pumps for efficiency involves a combination of engineering principles, advanced materials, and innovative technologies that cater specifically to the demands of petrochemical facilities.
KR-R-045D-LS-20-14-NN-N-3-K2AG-A6N-AAA-NNN-NNN
KRR045DLS2014NNN3K2AGA6NAAANNNNNN
When initiating the design process, engineers must first consider the unique operating conditions within petrochemical facilities. These environments often involve high pressures, varying temperatures, and the presence of various chemicals that could interact with pump materials. Therefore, selecting the appropriate materials is vital. Robust synthetic materials and corrosion-resistant alloys often form the basis of hydraulic oil pumps, ensuring durability and longevity even in harsh conditions.
83063965
One of the key design aspects is the pump configuration itself. Positive displacement pumps, which operate by trapping a fixed amount of fluid and forcing it into the discharge pipe, are often favored in petrochemical applications. They provide a constant and reliable flow rate, crucial for processes that require precision. Within this category, gear pumps and piston pumps are widely used. Each type has its advantages; for instance, gear pumps are typically more compact and easier to maintain, while piston pumps can handle higher pressures.
To enhance fluid control and operational efficiency, integration of smart technology into pump design is becoming increasingly important. Implementing sensors that monitor flow rates, pressure, and temperature allows operators to make real-time adjustments, optimizing performance. Additionally, the use of predictive maintenance tools can help prevent downtime by alerting operators to potential failures before they occur.
Energy efficiency is another significant consideration in the design of hydraulic oil pumps. In the quest to minimize operational costs and environmental impact, manufacturers are exploring variable frequency drives (VFDs) that adjust pump speed according to the system’s current demands. This not only reduces energy consumption but also decreases wear and tear on pump components, leading to longer service life and lower maintenance costs.
Furthermore, the integration of advanced simulation tools in the design process allows engineers to model fluid dynamics within the pump. Computational fluid dynamics (CFD) simulations enable designers to analyze how fluids behave under different conditions, leading to better-informed decisions regarding pump geometry and component selection. This technological advancement contributes to the creation of pumps that are not only efficient but also capable of handling diverse fluid properties commonly encountered in petrochemical applications.
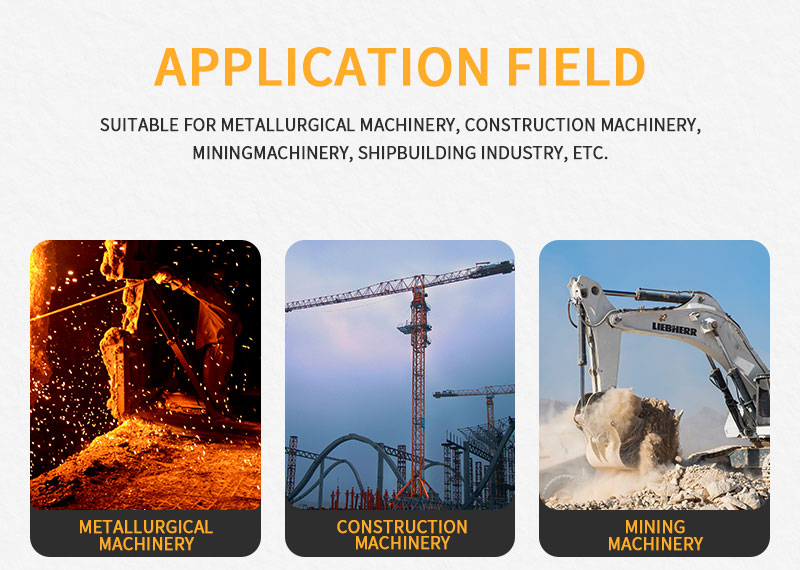
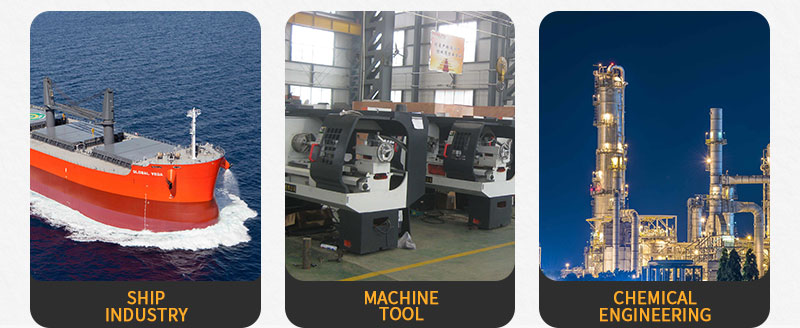