90L055HF5BB80R4C6C03GBA404024 high pressure pump
90L055HF5BB80R4C6C03GBA404024 high pressure pump
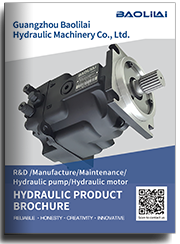
- Product Details
- Applicable Scene
The rapid advancement of technology in the field of robotics has led to the increasing integration of collaborative robotic systems, commonly known as cobots, into various industries. These systems are designed to work alongside human operators, enhancing productivity and safety. A crucial component that can significantly impact the effectiveness and efficiency of cobots is their hydraulic system, particularly the hydraulic oil pumps that facilitate precise motion and control. In this article, we will explore the design considerations for hydraulic oil pumps specifically tailored for collaborative robotic systems.
90-L-055-HF-5-BB-80-R-4-C6-C-03-GBA-40-40-24
90L055HF5BB80R4C6C03GBA404024
One of the primary challenges in designing hydraulic oil pumps for cobots is ensuring compatibility with the delicate nature of human-robot collaboration. Cobots are engineered to work in close proximity to human workers, meaning that the hydraulic systems must be not only efficient but also safe. This requires a careful balance between power output and operational speed, allowing the cobot to perform tasks quickly while minimizing the risk of injury to human operators.
701167
To achieve this, designers must consider the selection of materials and components that can withstand the pressures typically associated with hydraulic systems, while also ensuring that they are lightweight. The weight of the hydraulic pump influences the overall mobility of the cobot. Thus, utilizing advanced materials such as aluminum alloys or composite materials can provide the needed strength without unnecessary bulk.
Another critical aspect of hydraulic oil pump design is the integration of smart technology. Employing sensors and IoT capabilities can greatly enhance the performance of hydraulic pumps in collaborative robotic systems. For instance, real-time monitoring of hydraulic fluid levels, temperature, and pressure can ensure optimal performance and enable predictive maintenance. These capabilities not only prolong the lifespan of hydraulic components but also improve the reliability of the cobot in a working environment.
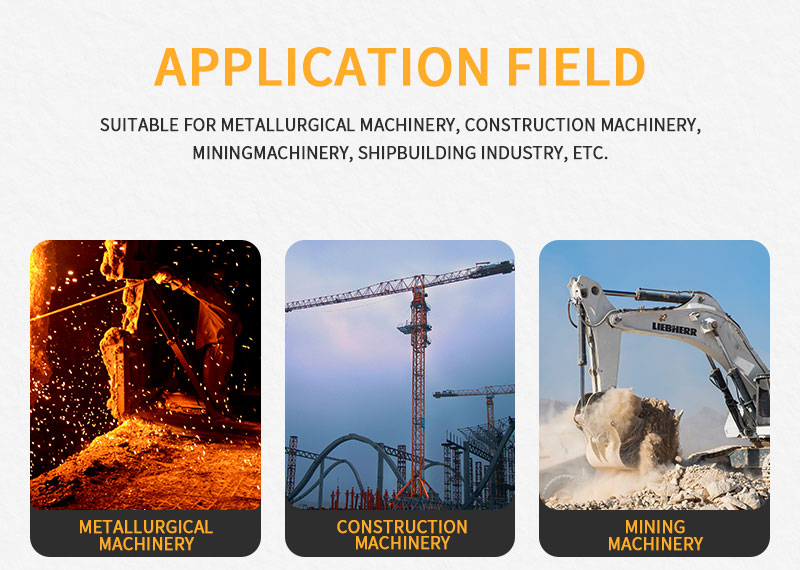
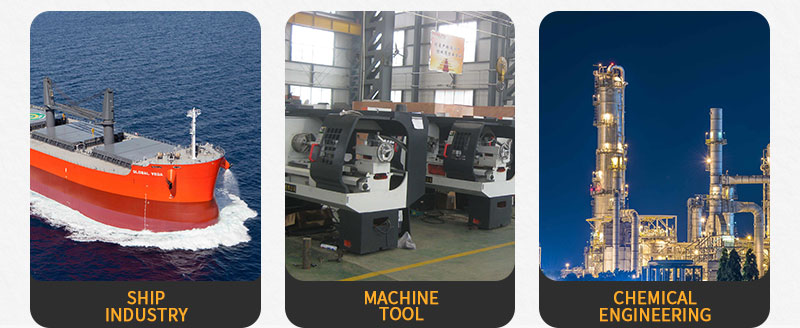