90L130KP5CD80R3F1H03GBA292924 sauer danfoss pump
90L130KP5CD80R3F1H03GBA292924 sauer danfoss pump
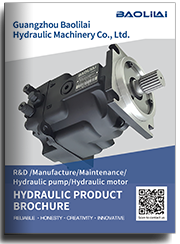
- Product Details
- Applicable Scene
Hydraulic pumps play a critical role in fluid circuits used for fluid handling in automotive manufacturing. Their efficient operation is essential for maintaining productivity and ensuring high-quality production. Unfortunately, hydraulic pump failures can lead to significant downtime, increased maintenance costs, and compromised product quality. Therefore, it is crucial to implement strategies that can prevent such failures. Here are several effective approaches to maintaining the reliability of hydraulic pumps in automotive fluid handling processes.
90-L-130-KP-5-CD-80-R-3-F1-H-03-GBA-29-29-24
90L130KP5CD80R3F1H03GBA292924
One of the primary causes of hydraulic pump failure is contamination. Dirty fluids can cause wear and tear on pump components, leading to premature failure. To mitigate this risk, regular filtration and purification of hydraulic fluids should be a priority. Installing high-quality filters and checking their conditions frequently can help to capture contaminants before they enter the pump. Additionally, ensuring that all hoses, connections, and storage tanks are clean and free of debris will further reduce the likelihood of contamination.
83037136
Another critical factor is proper fluid levels and selection. Low fluid levels can lead to pump cavitation, resulting in damage over time. It is vital to monitor fluid levels regularly and ensure that the reservoir is maintained at optimal levels. Furthermore, selecting the appropriate hydraulic fluid is crucial; it should meet the manufacturer’s specifications in terms of viscosity, lubrication properties, and thermal stability. Using the wrong fluid can lead to increased wear and suboptimal performance.
Regular maintenance and inspections are indispensable for preventing pump failures. Establishing a routine maintenance schedule that includes checking pump performance, looking for signs of leaks, and inspecting seals and bearings can identify potential problems before they escalate. Additionally, keeping detailed records of maintenance activities can help identify trends and inform future improvement measures.
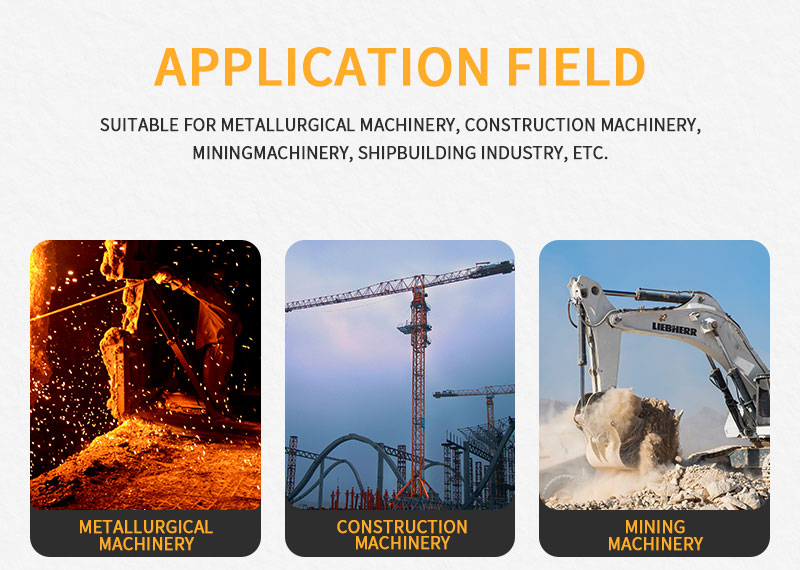
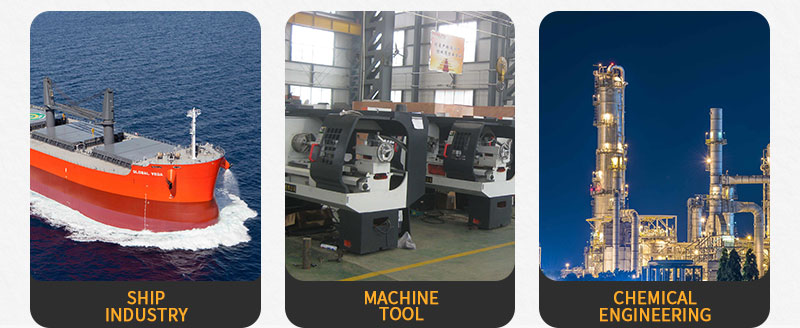