90R100KP1AB80P3S1F00GBA323224 hydraulic oil pump
90R100KP1AB80P3S1F00GBA323224 hydraulic oil pump
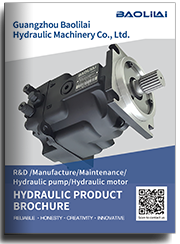
- Product Details
- Applicable Scene
In various industrial applications, plunger pumps play a crucial role in the efficient transfer of liquids, including corrosive substances and high-viscosity fluids. As technology progresses, the demand for higher performance standards continues to rise, prompting the exploration of advanced materials that enhance the durability and effectiveness of these pumps. This article delves into the innovations shaping the future of plunger pump materials, focusing on their implications for durability and overall performance.
90-R-100-KP-1-AB-80-P-3-S1-F-00-GBA-32-32-24
90R100KP1AB80P3S1F00GBA323224
The traditional materials used in plunger pumps range from stainless steel to various plastics, each offering a different balance of strength, corrosion resistance, and wear characteristics. However, the limitations of these conventional materials have inspired researchers and engineers to seek alternatives that can provide enhanced durability under extreme operating conditions.
83012969
One of the most promising advancements in this field is the development of composite materials that combine the best properties of various substances. By leveraging advanced polymer technology, manufacturers can create composites that exhibit exceptional resistance to chemical attack while maintaining lightweight and high-strength characteristics. These composite materials can withstand significant stress and thermal variations, ensuring the longevity of plunger pumps even in the most challenging environments.
Additionally, the advancement of ceramics and ceramic composites has opened new avenues for improving plunger pump durability. These materials are incredibly hard and resistant to wear, making them ideal for applications involving abrasive fluids. Furthermore, their inherent resistance to chemical corrosion makes them perfect candidates for handling harsh substances without degradation. As production techniques continue to improve, the integration of ceramic materials into plunger pumps may become more feasible and widespread.
Another significant trend influencing the future of plunger pump materials is the growing adoption of additive manufacturing, or 3D printing. This technology allows for the creation of complex geometries and tailored material compositions that were previously impossible to achieve through traditional manufacturing methods. With additive manufacturing, it is possible to design pump components with enhanced surface structures that reduce friction and wear, thus prolonging the operational life of the equipment.
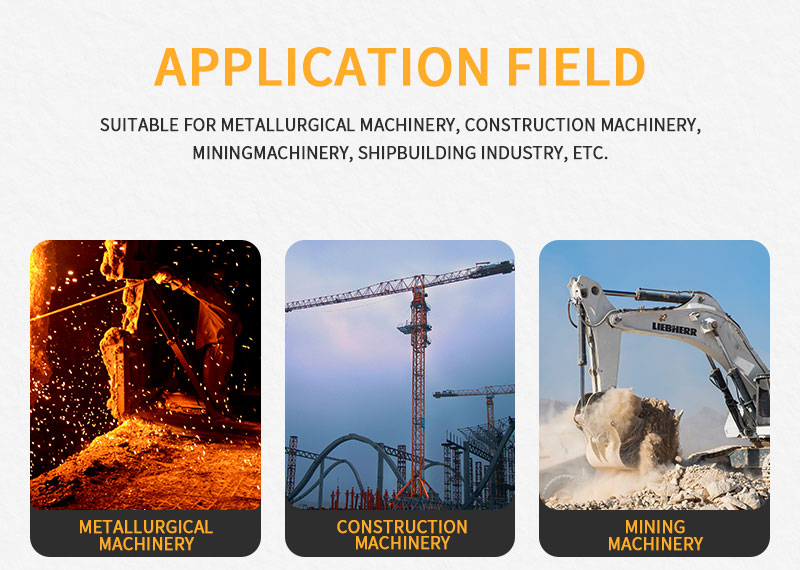
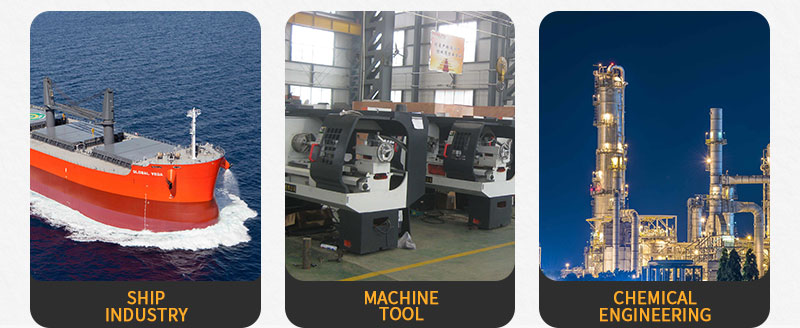