KRR045DLS2120NNN3C2BGA6NPLBNNNNNN danfoss pump
KRR045DLS2120NNN3C2BGA6NPLBNNNNNN danfoss pump
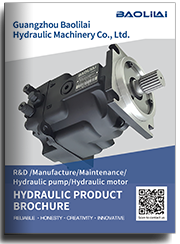
- Product Details
- Applicable Scene
The design of hydraulic oil pumps is a critical aspect of engineering when it comes to heavy-duty locomotives and freight transport systems. These pumps play a vital role in ensuring the efficient operation of hydraulic systems, which are essential for various locomotive functionalities, including propulsion, braking, and other auxiliary services. In this article, we will explore the key considerations, challenges, and innovations involved in designing hydraulic oil pumps for this demanding application.
KR-R-045D-LS-21-20-NN-N-3-C2BG-A6N-PLB-NNN-NNN
KRR045DLS2120NNN3C2BGA6NPLBNNNNNN
Hydraulic oil pumps must be able to withstand the harsh operating conditions encountered in heavy-duty applications. High pressures, fluctuating temperatures, and continuous operation are standard in locomotive environments, necessitating pumps that are robust and reliable. Therefore, selecting the right materials is crucial. Durable metals such as high-strength steel or aluminum alloys are often chosen for their mechanical properties and resistance to wear and corrosion. Additionally, protective coatings can enhance the lifespan of the pump components.
7004159S
Another vital consideration is the design of the pump configuration itself. Gear pumps, vane pumps, and piston pumps are common types used in hydraulic applications, each with its advantages and limitations. Gear pumps are known for their simplicity and reliability, making them suitable for high-pressure applications. Vane pumps, on the other hand, can offer better efficiency at lower pressures, while piston pumps are often employed in situations requiring a high degree of precision and control. Understanding the specific application requirements will guide engineers in selecting the most appropriate pump type.
Efficiency is a primary concern in the design of hydraulic pumps, particularly in large-scale freight operations where fuel economy can significantly impact overall operational costs. The integration of advanced technologies such as variable displacement controls and electronic management systems can optimize flow and pressure, improving the efficiency of hydraulic systems. By minimizing energy losses and tailoring the pump operation to the load demands, significant savings can be realized over the operational life of the locomotive.
Noise and vibration control are also critical in the design process. Hydraulic systems can generate significant noise levels, which can be detrimental to both operator comfort and regulatory compliance. Advances in hydraulic fluid formulations and pump design can help mitigate noise and vibration, ensuring a smoother operation. For example, using advanced materials that provide better damping characteristics or designing pumps to reduce cavitation can lead to quieter systems.
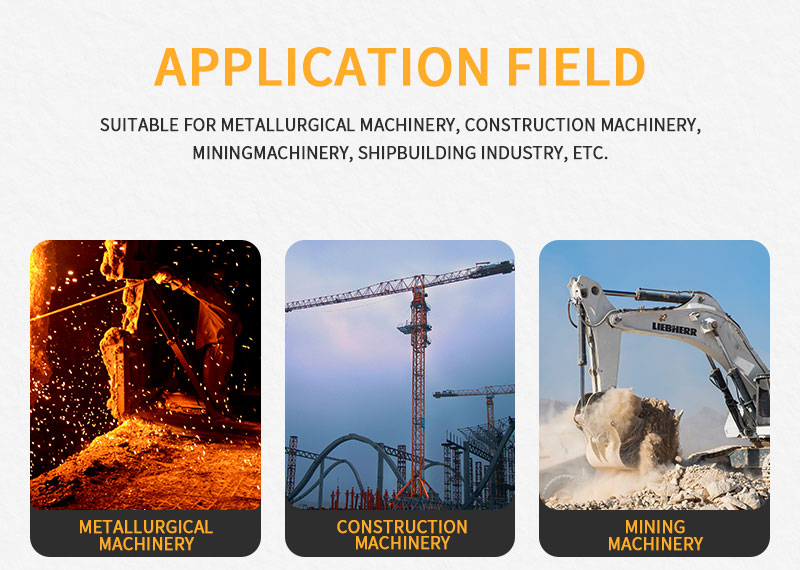
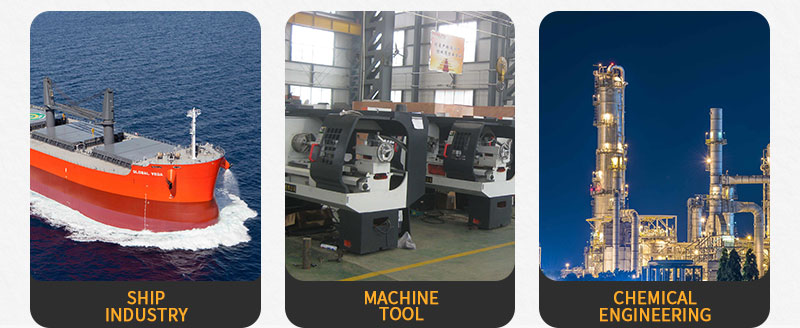