KRR045DLS1420NNN3K2NFA6NAAANNNNNN hydraulic pump
KRR045DLS1420NNN3K2NFA6NAAANNNNNN hydraulic pump
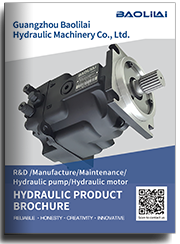
- Product Details
- Applicable Scene
The construction industry requires robust and efficient systems for the handling and transportation of bricks and blocks. One crucial component in these automated systems is the hydraulic oil pump, which plays a significant role in powering various machinery, including conveyors, lifts, and automated guided vehicles (AGVs). This article will explore the key considerations in designing hydraulic oil pumps tailored for automated brick and block handling systems.
KR-R-045D-LS-14-20-NN-N-3-K2NF-A6N-AAA-NNN-NNN
KRR045DLS1420NNN3K2NFA6NAAANNNNNN
Hydraulic systems offer several advantages over mechanical systems, including high force transmission, precise control, and flexibility. However, to maximize these benefits in brick and block handling applications, careful design and selection of hydraulic oil pumps are essential.
83060425
First and foremost, determining the specifications of the hydraulic pump is critical. This involves calculating the required flow rate and pressure needed to perform the desired operations efficiently. For handling heavy materials like bricks and blocks, the pump must generate sufficient pressure to lift and transport loads safely. Engineers must consider the weight of the materials, the height and distance of lifting and conveying, while also accounting for dynamic forces that may occur during operation.
Next, selecting the right type of hydraulic pump is vital. Common types include gear pumps, vane pumps, and piston pumps, each with distinct characteristics. Gear pumps are known for their simplicity and efficiency at lower pressures, while piston pumps provide higher pressure capabilities and flow rates, making them suitable for heavy-duty applications. For automated brick and block handling systems, piston pumps often prove to be the best choice due to their ability to handle high pressures and provide consistent performance under varying load conditions.
Moreover, the design of the pump system must ensure compatibility with the hydraulic fluids used. Hydraulic oil plays a crucial role in lubrication and cooling; hence, selecting an appropriate oil grade that can withstand the operational temperatures and conditions is essential. Compatibility with seals and other materials used in the pump system is also vital to prevent leaks and ensure durability.
Incorporating advanced control systems is another key aspect of pump design. Modern automated systems benefit from electronic control units (ECUs) that allow for precise monitoring and adjustment of hydraulic operations. Implementing sensors to monitor pressure, temperature, and flow rates can enhance system efficiency and prevent failures. Such automation not only improves safety by reducing human intervention but also optimizes energy consumption, leading to reduced operational costs.
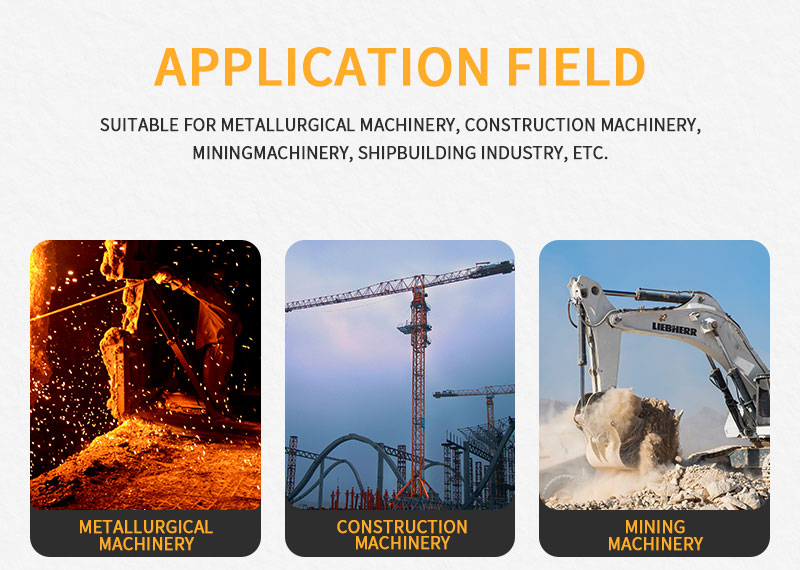
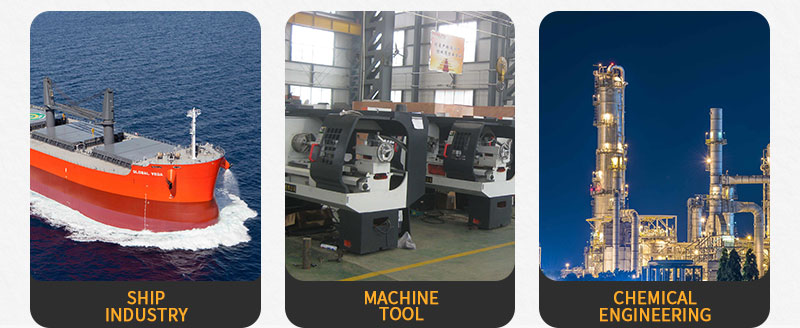