KRR045DLS2116NNN3C3NFA6NPLBNNNNNN high pressure pump
KRR045DLS2116NNN3C3NFA6NPLBNNNNNN high pressure pump
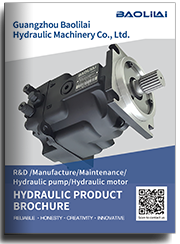
- Product Details
- Applicable Scene
The frozen food industry is a critical segment of the food processing sector, requiring advanced technology and machinery to maintain product quality and safety. Among the essential components in this industry are hydraulic oil pumps, which play a vital role in powering various equipment. To ensure optimal performance in frozen food processing, the design of these hydraulic oil pumps must be approached with precision and foresight.
KR-R-045D-LS-21-16-NN-N-3-C3NF-A6N-PLB-NNN-NNN
KRR045DLS2116NNN3C3NFA6NPLBNNNNNN
Hydraulic oil pumps are responsible for converting mechanical energy into hydraulic energy, which is then used to power hydraulic systems within the processing equipment. The design phase must take into account several factors, including temperature control, efficiency, durability, and maintenance.
80004245
One of the primary challenges in designing hydraulic oil pumps for frozen food processing is the extreme operating conditions. Equipment must function efficiently at low temperatures, as food products need to be processed and stored in frozen states. This requires the selection of materials that can withstand low temperatures without becoming brittle or losing mechanical integrity. Additionally, the hydraulic oil itself must be formulated to remain effective under cold conditions, preventing viscosity issues that could impede pump performance.
Efficiency is paramount in the frozen food processing industry due to the high volume of product that needs to be handled quickly while maintaining quality. Hydraulic oil pumps should be designed for high flow rates and pressures to ensure that machinery operates smoothly. Incorporating technology such as variable displacement pumps can enhance efficiency, allowing the pump output to adjust to the demands of the system dynamically. This feature helps to save energy and reduces wear on the pump components, translating into lower operational costs.
Durability is another crucial aspect of the design process. Frozen food processing environments can be harsh, with equipment often exposed to moisture and chill. The pump design must incorporate seals and protective coatings that minimize the risk of corrosion and wear over time. Regular maintenance cycles should also be considered during the design phase, with features that facilitate easy access to components for inspection and repairs.
Furthermore, safety and compliance with food industry regulations are imperative in the design of hydraulic oil pumps. Materials used in the pumps must meet food safety standards to avoid contamination, and the design should minimize chances of leaks, which could pose health risks. Incorporating fail-safes and alarms to detect irregularities in pump performance can further enhance the safety of the frozen food processing equipment.
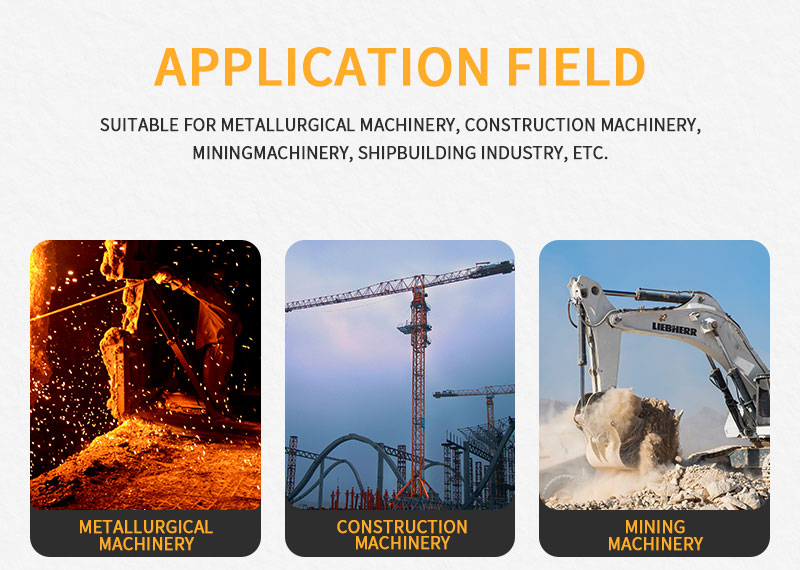
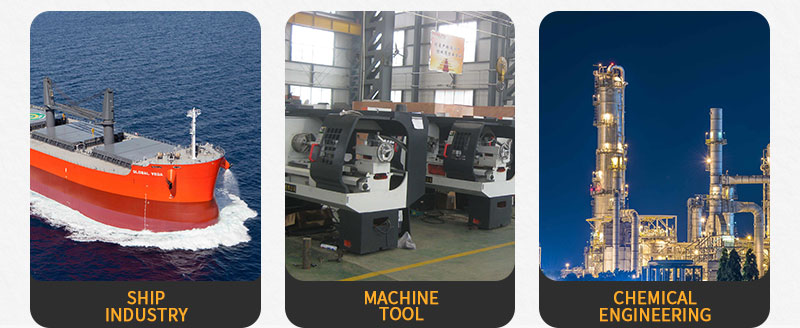