KRR045DLS1420NNN3C2NFA6NAAANNNNNN sauer danfoss pump
KRR045DLS1420NNN3C2NFA6NAAANNNNNN sauer danfoss pump
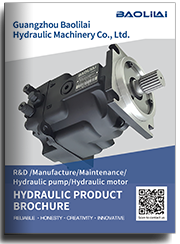
- Product Details
- Applicable Scene
The hydraulic system of an aircraft plays a crucial role in its overall functionality, particularly in controlling the landing gear. Effective testing and evaluation of landing gear systems require sophisticated hydraulic oil pumps that can accurately simulate real-world operational conditions. This article examines the design considerations and requirements for hydraulic oil pumps used in aircraft landing gear testing and evaluation.
KR-R-045D-LS-14-20-NN-N-3-C2NF-A6N-AAA-NNN-NNN
KRR045DLS1420NNN3C2NFA6NAAANNNNNN
Hydraulic oil pumps are essential components in simulating the operational pressures and flows experienced by landing gear during aircraft operations. Their primary objective is to provide precise control over hydraulic fluid delivery to actuators, ensuring that all parameters of the landing gear system can be evaluated effectively. To achieve this, several design factors must be addressed.
83049171
One of the key considerations in designing hydraulic oil pumps is the required flow rate and pressure range. Different aircraft models have varying hydraulic specifications, which necessitates that the pump’s design aligns with the specific needs of the landing gear being tested. Designers must conduct a thorough analysis of the landing gear system’s operational profiles to determine the necessary flow rates and pressure thresholds. This ensures that the pump can adequately replicate real-life scenarios encountered during takeoff, landing, and ground operations.
Another important aspect is the pump’s efficiency and reliability. The hydraulic oil pumps must be designed to minimize energy consumption while maximizing flow delivery. Utilizing advanced materials and efficient pump geometries can enhance the overall performance. Additionally, the reliability of the pump is critical, as any failure during testing can lead to inaccurate evaluations and potentially costly setbacks. Implementing redundancy measures, fail safes, and robust testing protocols can help ensure the longevity and dependability of these pumps.
Noise and vibration levels are also vital considerations in pump design, especially in a laboratory setting where precision testing is paramount. Hydraulic oil pumps must operate quietly to avoid interference with sensitive testing equipment and to ensure that any anomalies detected during testing can be traced accurately to their source without additional noise complicating the results.
Moreover, integrating advanced control systems into hydraulic pumps allows for real-time monitoring and adjustments to be made during testing. This can include computer-controlled flow rate changes, pressure adjustments, and feedback input from the testing setup. Such integration enhances the versatility of the oil pumps and allows engineers to simulate a broader range of operational conditions, ultimately leading to more comprehensive testing and evaluation outcomes.
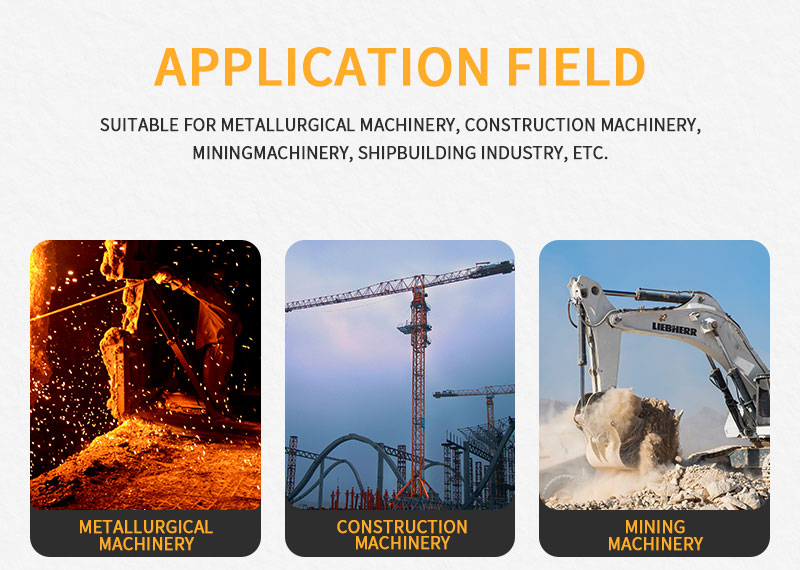
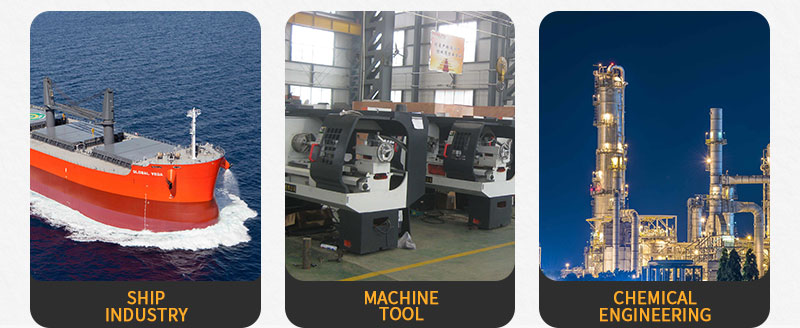