ERL147CLS1210NNF3S1RPA1NAAANNNNNN hydraulic pump
ERL147CLS1210NNF3S1RPA1NAAANNNNNN hydraulic pump
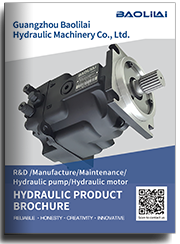
- Product Details
- Applicable Scene
Cavitation in hydraulic pumps is a significant challenge faced in fluid systems, especially in the oil and gas exploration sector. When the pressure within a hydraulic pump drops below a certain threshold, vapor bubbles form, which can result in a range of problems, including reduced efficiency, damage to the pump, and operational failures. Understanding how to identify and mitigate cavitation is crucial for the longevity and performance of hydraulic systems in this demanding industry.
ER-L-147C-LS-12-10-NN-F-3-S1RP-A1N-AAA-NNN-NNN
ERL147CLS1210NNF3S1RPA1NAAANNNNNN
Understanding Cavitation
83043702
Cavitation occurs when the pressure in a fluid drops below its vapor pressure, causing vapor pockets or bubbles to form. These bubbles can collapse violently when they move to areas of higher pressure, leading to shock waves that can cause significant damage to the pump components, including erosion of metal surfaces. In oil and gas exploration, where hydraulic systems are used for various applications such as drilling and fluid transport, cavitation can lead to increased maintenance costs, unscheduled downtime, and compromised safety.
Identifying Cavitation
To effectively address cavitation, it is essential to first identify its symptoms. Common indicators include:
Unusual noise or vibration from the pump
Fluctuating pressure readings
Decreased flow rates
Increased power consumption
Monitoring these signs can help operators detect cavitation early, preventing more severe damage.
Causes of Cavitation
There are several factors that can lead to cavitation in hydraulic systems:
Suction Pressure: Low suction pressure can lead to cavitation. Ensuring that the pump intake has sufficient fluid can mitigate this risk.
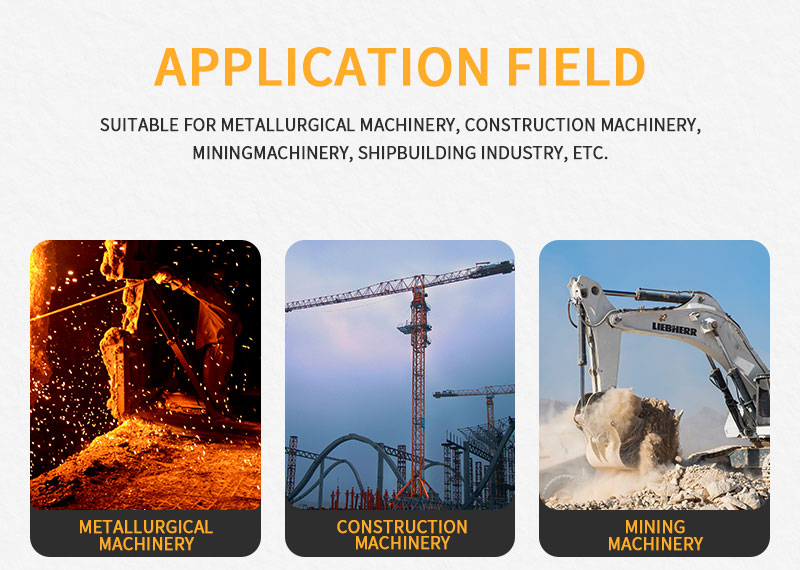
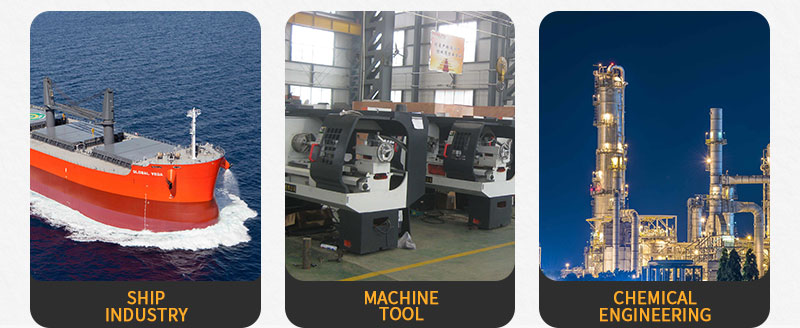