ERL147CFF2520NNN3S1RPA1NNNNNNNNNN hydraulic oil pump
ERL147CFF2520NNN3S1RPA1NNNNNNNNNN hydraulic oil pump
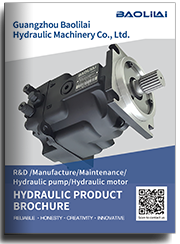
- Product Details
- Applicable Scene
Cavitation is a common issue in hydraulic systems that can lead to severe damage and reduced efficiency of pumps, particularly in heavy industrial equipment. Understanding and mitigating cavitation is critical for maintaining system performance and ensuring the longevity of hydraulic components. This article explores the causes of cavitation, its effects, and effective strategies to resolve the problem.
ER-L-147C-FF-25-20-NN-N-3-S1RP-A1N-NNN-NNN-NNN
ERL147CFF2520NNN3S1RPA1NNNNNNNNNN
Cavitation occurs when the pressure in a hydraulic fluid drops below the vapor pressure, causing the fluid to vaporize and form bubbles. These bubbles can collapse violently when they move into higher pressure areas, resulting in shock waves that can erode or damage pump components. Common causes of cavitation in hydraulic pumps include:
83041122
Low inlet pressure: Insufficient fluid pressure at the pump inlet can cause a drop in pressure, leading to cavitation.
High fluid temperature: Increased temperatures decrease the fluid’s density and raise the vapor pressure, making it easier for cavitation to occur.
Excessive flow resistance: Factors such as blocked filters, inadequate piping design, and bends in the fluid path can create additional resistance that lowers inlet pressure.
Incorrect pump selection: Using a pump with inadequate capacity or one not suited for the application can exacerbate cavitation issues.
To effectively solve hydraulic pump cavitation, consider the following strategies:
Maintain Adequate Inlet Pressure: Ensure that the hydraulic system maintains proper fluid levels and is free from leaks. Utilize appropriate reservoir sizes and keep them filled to generate adequate pressure at the pump inlet.
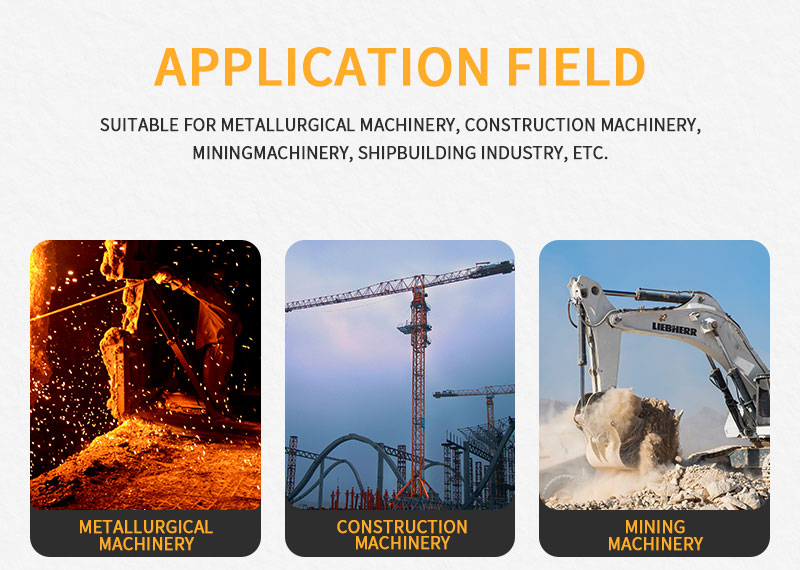
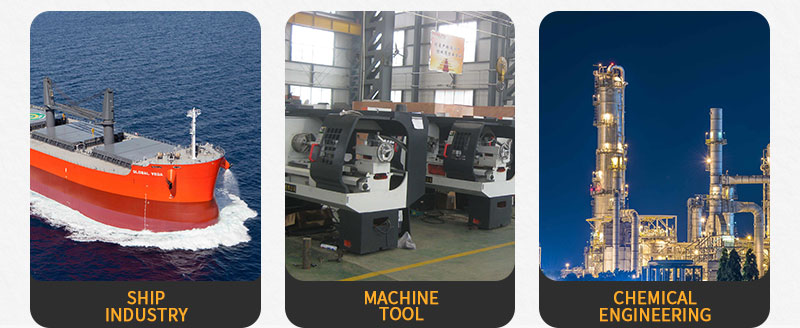