KRR045DLS1914NNN3K1NRA6NAAANNNNNN hydraulic pump
KRR045DLS1914NNN3K1NRA6NAAANNNNNN hydraulic pump
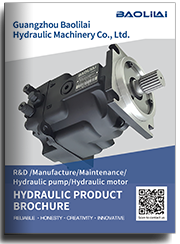
- Product Details
- Applicable Scene
The utilization of hydraulic oil pumps in crawler and track-type construction equipment is critical for the effective operation of various functions such as lifting, pushing, and digging. These hydraulic systems enable heavy machinery to perform demanding tasks, and designing the right hydraulic oil pump is essential to ensure efficiency, durability, and reliability.
KR-R-045D-LS-19-14-NN-N-3-K1NR-A6N-AAA-NNN-NNN
KRR045DLS1914NNN3K1NRA6NAAANNNNNN
When designing hydraulic oil pumps for these types of equipment, several key factors must be taken into account. First and foremost is the pump’s capacity. The pump must deliver the correct flow rate and pressure to meet the operational requirements of the machine. The flow rate must be sufficient to provide the necessary speed for hydraulic actuators, while the pressure must be adequate to support tasks such as digging or lifting heavy loads.
83007118
Another essential aspect of hydraulic pump design is efficiency. Hydraulic systems inherently deal with energy loss through heat generation, so designers must focus on minimizing these losses. This can be achieved by selecting high-quality materials, optimizing the pump’s geometry, and ensuring close tolerances between moving components. Using variable displacement pumps can also enhance efficiency, as they allow the flow rate to be adjusted based on the load, thereby saving energy during lighter operations.
Durability and reliability are also critical considerations, given the harsh working conditions faced by crawler and track-type equipment. Hydraulic pumps must withstand extreme temperatures, pressures, and potential contamination from dust and debris. Selecting robust materials and implementing effective sealing systems can help protect the internal components from wear and tear. Additionally, incorporating advanced monitoring systems can facilitate real-time tracking of pump performance, enabling timely maintenance and reducing the risk of unexpected failures.
Another significant design consideration is the integration of hydraulic circuits. The pump must be designed to work seamlessly with other hydraulic components, such as valves, actuators, and filters. Careful planning of the hydraulic circuit layout can optimize performance and enhance the overall functionality of the equipment. Furthermore, it is vital to ensure that the hydraulic system is designed with flexibility in mind, allowing for future upgrades or modifications as technology advances or operational needs change.
In recent years, environmentally friendly designs have gained traction in the industry. Designers are increasingly focusing on creating pumps that consume less energy and use biodegradable hydraulic fluids. Using electric or hybrid power sources can also contribute to reducing the environmental impact of construction equipment.
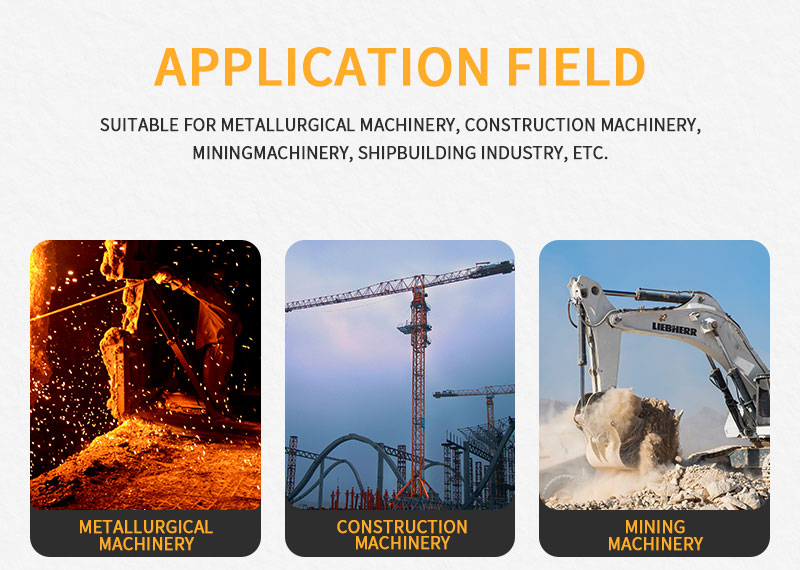
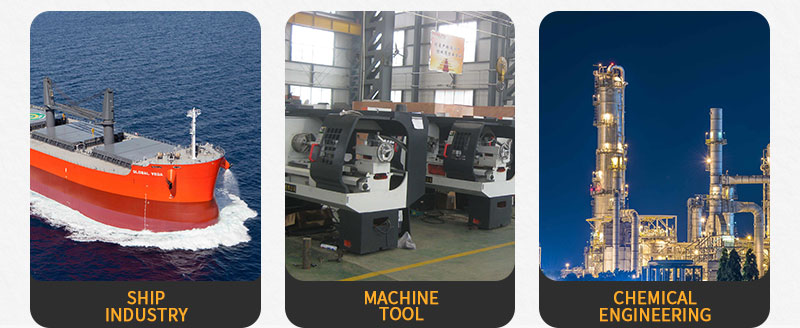