90K075NC0N7N0S1W00NNN0000F0 danfoss motor
90K075NC0N7N0S1W00NNN0000F0 danfoss motor
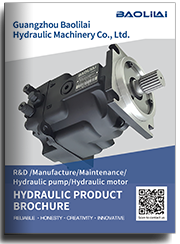
- Product Details
- Applicable Scene
The aerospace industry relies heavily on advanced technologies to ensure the safety, efficiency, and performance of aircraft. Hydraulic motors are one of the pivotal components in many aerospace applications, providing the necessary power for various operations, including flight control systems, landing gear, and braking systems. However, the application of hydraulic motors in aerospace presents several key challenges that engineers and manufacturers need to address to optimize performance and reliability.
90-K-075-NC-0-N-7-N-0-S1-W-00-NNN-00-00-F0
90K075NC0N7N0S1W00NNN0000F0
One of the most significant challenges in the use of hydraulic motors in aerospace is weight. The aviation sector is highly sensitive to weight, as it directly impacts fuel efficiency, payload capacity, and overall operational costs. Hydraulic systems, while powerful and efficient, can be bulky and add considerable weight to the aircraft. Engineers must design hydraulic motors that maximize performance while minimizing weight. This often involves using advanced materials, such as composites and lightweight alloys, and optimizing the design to reduce size and mass without compromising strength and reliability.
11177395
Another critical challenge is the extreme environmental conditions encountered during flight. Hydraulic motors must operate effectively under a wide range of temperatures, altitudes, and pressures. For instance, temperatures can vary significantly, from extreme cold at high altitudes to high heat during operation on the ground. Moreover, hydraulic fluids can behave differently under varying pressures and temperatures, potentially affecting the performance of the motor. Addressing these environmental factors requires rigorous testing and the development of specialized hydraulic fluids that can maintain their properties across the operational range.
Reliability and maintenance also pose significant challenges. Given the critical role of hydraulic systems in ensuring the safety and functionality of aircraft, any failure can have catastrophic consequences. Therefore, hydraulic motors must be designed for maximum reliability, with robust sealing and low wear components to ensure long service life. Additionally, maintenance protocols need to be developed that allow for quick inspections and repairs without significant downtime. This challenge is compounded by the need to predict potential failures before they occur, which requires advanced monitoring and diagnostic systems.
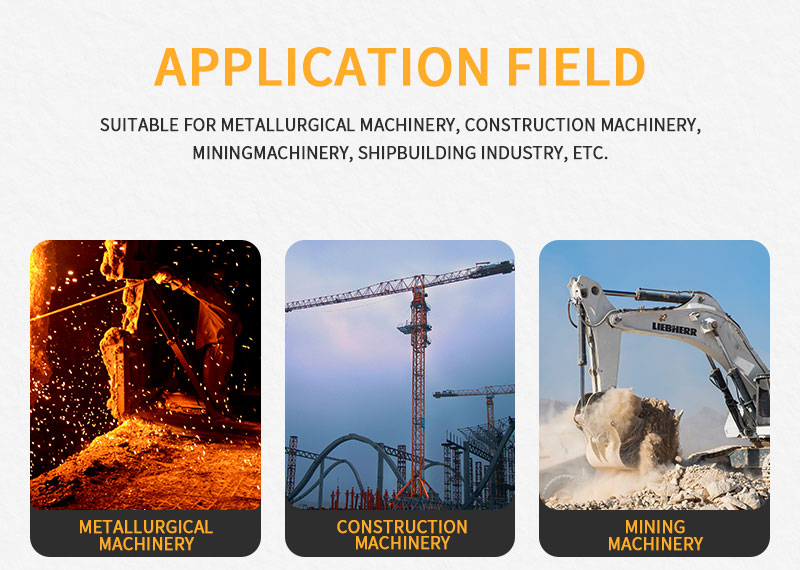
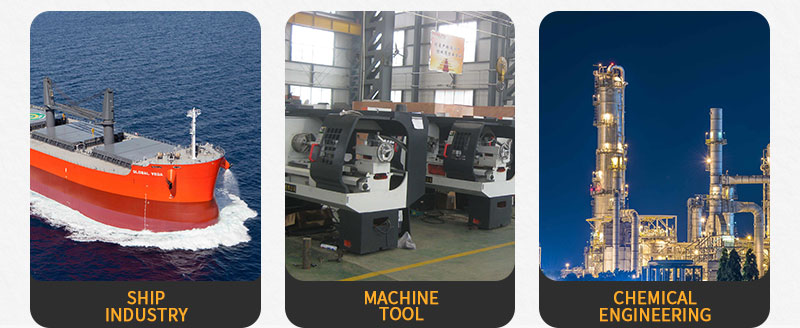