90K055NC0N8N0S1W00EBA0000E4 piston motor
90K055NC0N8N0S1W00EBA0000E4 piston motor
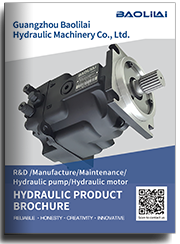
- Product Details
- Applicable Scene
Piston engines have long been a staple in the automotive and aerospace industries, serving as the backbone of many vehicles and machines. As technology and engineering practices have evolved, so too have the materials used in the construction of these engines. The modern piston engine incorporates a variety of innovative materials that enhance performance, durability, and efficiency while minimizing weight and environmental impact. This article explores some of the key materials that are shaping the future of piston engine design.
90-K-055-NC-0-N-8-N-0-S1-W-00-EBA-00-00-E4
90K055NC0N8N0S1W00EBA0000E4
One notable trend in modern piston engines is the increased use of lightweight alloys. Traditional cast iron and steel components, while strong, are often heavier than their modern counterparts. Aluminum alloys, for example, are being utilized for engine blocks, cylinder heads, and pistons. These materials provide comparable strength while significantly reducing the overall weight of the engine. The lighter weight contributes to improved fuel efficiency and better handling characteristics in vehicles.
9431516
Another innovative material making waves in piston engine design is carbon fiber. Renowned for its exceptional strength-to-weight ratio, carbon fiber is increasingly being integrated into engine components such as crankshafts and connecting rods. These components benefit from the rigidity and lightweight properties of carbon fiber, allowing for higher RPMs and improved performance without the penalty of increased mass. Moreover, carbon fiber components can withstand higher temperatures and stresses, contributing to the longevity of the engine.
Advanced composites are also gaining traction in the development of piston engines. These materials blend various fibers and resins to create lightweight, durable components. For example, piston skirts made from composite materials can reduce friction and wear, leading to better efficiency and lower emissions. Composites can also be engineered to provide thermal stability, allowing engines to operate at higher temperatures without compromising their integrity.
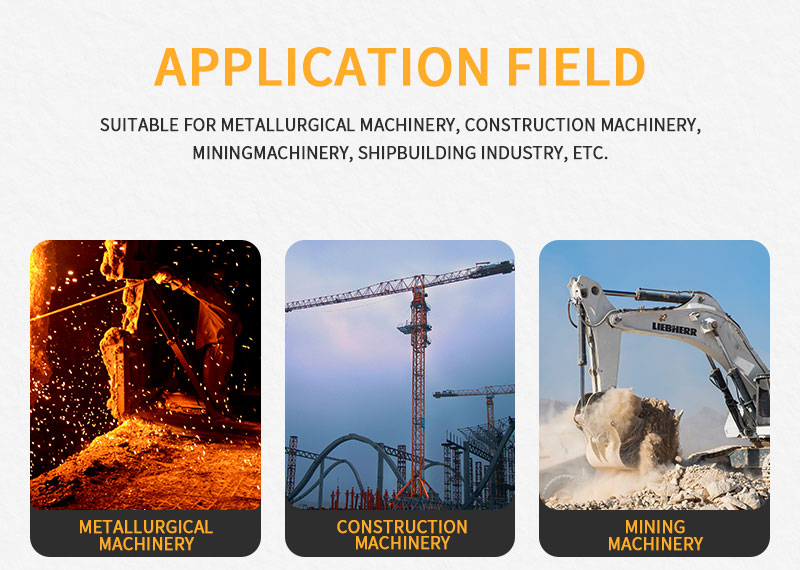
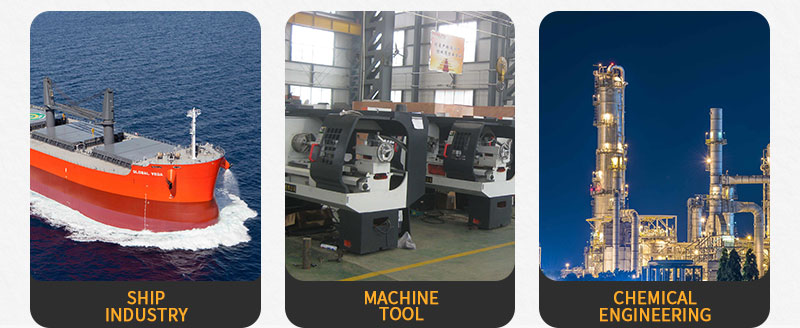