90K055NC0N7N0S1W00EBA0000F3 danfoss motor
90K055NC0N7N0S1W00EBA0000F3 danfoss motor
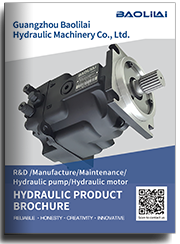
- Product Details
- Applicable Scene
The evolution of high voltage motor designs has significantly shaped various industries, from energy generation to manufacturing. As environmental concerns rise and energy efficiency demands increase, innovations in high voltage motor technology are more crucial than ever. This article explores the key advancements in the design and production of high voltage motors, highlighting the journey from initial concept to final manufacturing.
90-K-055-NC-0-N-7-N-0-S1-W-00-EBA-00-00-F3
90K055NC0N7N0S1W00EBA0000F3
One of the major innovations in high voltage motor design is the introduction of advanced materials. Traditional materials such as copper and aluminum are being enhanced with composite materials, which provide higher conductivity and greater durability. The use of lightweight yet strong materials not only improves performance but also reduces the overall weight of the motors. This is particularly important in applications where space and weight constraints are critical.
11136039
Another significant advancement is the implementation of digital technology in motor design. The advent of computer-aided design (CAD) software and simulation tools has revolutionized the way engineers approach motor design. These tools allow for precise modeling of the motor’s behavior under various operating conditions. As a result, engineers can optimize designs for efficiency and performance before moving to production. Predictive analytics also play a role in identifying potential issues early in the design phase, minimizing costly changes during manufacturing.
In addition to materials and technology, there has been a shift towards modular designs in high voltage motors. Modular motors allow manufacturers to create consistent, scalable designs that can be easily adapted for different applications. This approach not only speeds up the production process but also enables quicker customization based on specific customer requirements. Modularity in design can lead to reduced downtime during maintenance, as components can be easily replaced without needing to overhaul an entire system.
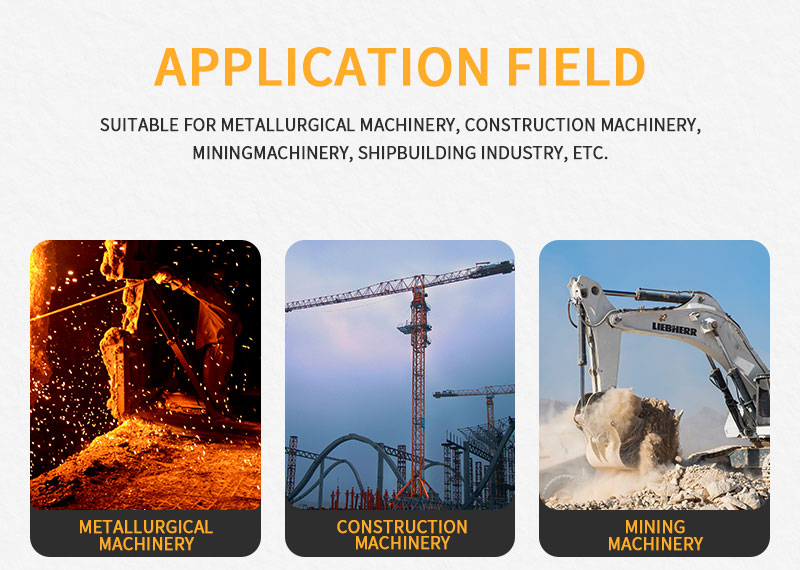
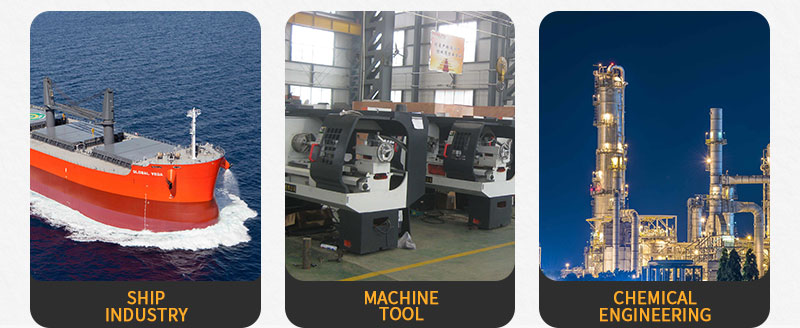