90R075KA5NN80P3C7D03GBA232324 danfoss pump
90R075KA5NN80P3C7D03GBA232324 danfoss pump
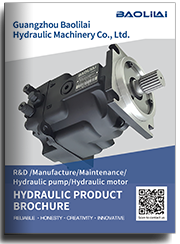
- Product Details
- Applicable Scene
In recent years, the demand for efficient and reliable methods of carbon dioxide (CO2) injection has surged, particularly in applications such as enhanced oil recovery, carbon sequestration, and various industrial processes. One of the critical components in these systems is the plunger pump, which is specifically designed to manage the high pressures and the unique properties of CO
90R075-KA-5-NN-80-P-3-C7-D-03-GBA-23-23-24
90R075KA5NN80P3C7D03GBA232324
Plunger pumps operate by utilizing a reciprocating mechanism that moves a plunger back and forth within a cylinder. This action creates a high-pressure environment that is capable of injecting fluids into more extensive systems. When it comes to CO2, the ability of plunger pumps to maintain high pressure while ensuring low maintenance and operational costs makes them an ideal choice.
83029782
One of the key advantages of using plunger pumps for high-pressure CO2 injection is their ability to deliver consistent flow rates. CO2, especially in its supercritical state, exhibits unique fluid dynamics. Plunger pumps can effectively accommodate these changes by adjusting their stroke lengths and speeds, ensuring that the desired flow rate and pressure are maintained even as conditions fluctuate.
Another significant benefit is their robustness and reliability in harsh operating environments. CO2 injection systems often face challenges such as temperature fluctuations, corrosive elements, and varying pressures. Plunger pumps are typically made from high-strength materials and are designed to withstand these conditions, leading to longer operational lifespans and reduced downtime.
However, the implementation of plunger pumps in high-pressure CO2 systems also requires careful consideration of safety measures. Given the high pressures involved and the potential hazards of CO2 leakage, it is crucial to ensure that all components of the injection system, including the pump, valves, and tubing, are rated for the specific conditions of operation. Regular maintenance and monitoring are essential to identify any wear or potential failure points before they lead to safety incidents.
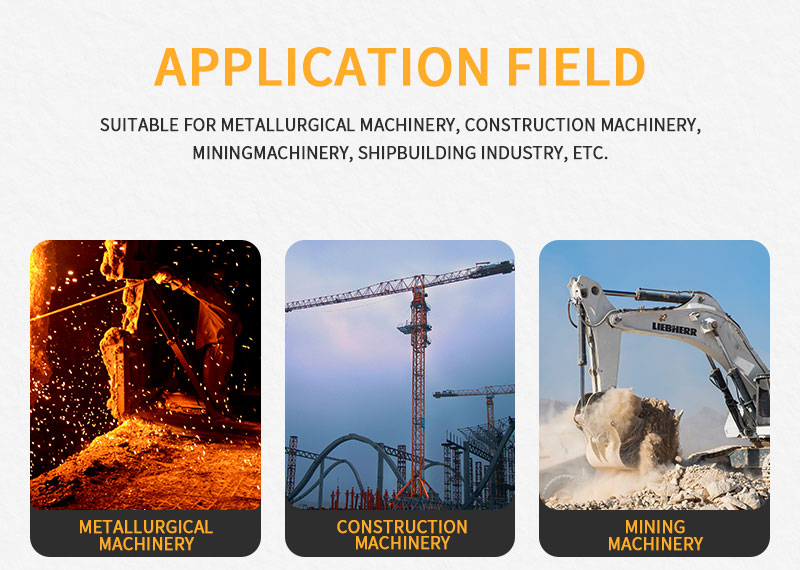
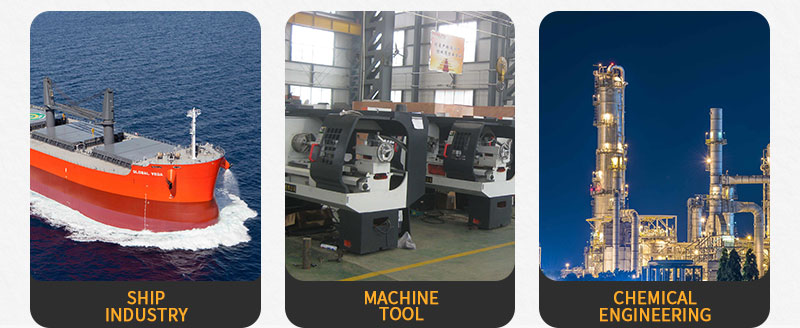