90L180KA5BC80SCC8J00NNN382330 sauer danfoss pump
90L180KA5BC80SCC8J00NNN382330 sauer danfoss pump
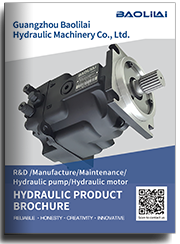
- Product Details
- Applicable Scene
Hydraulic pump systems are integral to a wide range of industrial equipment, providing the power needed to operate machines efficiently. However, contamination in these systems can lead to decreased performance, increased wear and tear, and ultimately, system failure. Understanding how to prevent and address hydraulic pump system contamination is essential for maintaining equipment reliability and longevity.
90-L-180-KA-5-BC-80-S-C-C8-J-00-NNN-38-23-30
90L180KA5BC80SCC8J00NNN382330
Firstly, it is crucial to recognize the sources of contamination. Contaminants can enter hydraulic systems through several avenues, including dirt and dust from the environment, wear particles from components, moisture, and improper fluid handling practices. To combat these issues, implementing a comprehensive contamination control strategy is essential.
702210
One of the most effective methods for reducing contamination is ensuring proper filtration. Installing high-efficiency filters specifically designed for hydraulic systems can significantly reduce the presence of particulates and other contaminants. Regularly inspecting and replacing filters is also crucial, as blocked or dirty filters can exacerbate contamination issues.
Additionally, maintaining clean fluid is fundamental. This involves using high-quality hydraulic fluids that are specifically formulated to resist contamination. Regular fluid analysis can help identify the presence of contaminants and determine when fluid replacement is necessary. The practice of “fluid cleanliness” should be rigorously adhered to during fluid changes to avoid introducing contaminants into the system.
Maintenance of the hydraulic system components is another critical aspect. Regular inspection of hoses, fittings, and connections can help identify leaks and areas where contamination might enter. Moreover, proper tightening of connections can prevent contamination from the outside environment. Equipment operators should be trained to recognize the signs of contamination, including unusual noises, fluctuating pressures, or decreased operational efficiency.
Training personnel on best practices for handling hydraulic systems is also essential for contamination prevention. Ensuring that employees understand the importance of cleanliness and the potential impacts of contamination can foster a culture of care and diligence. Emphasizing the need for proper storage and handling of hydraulic fluids and components is vital.
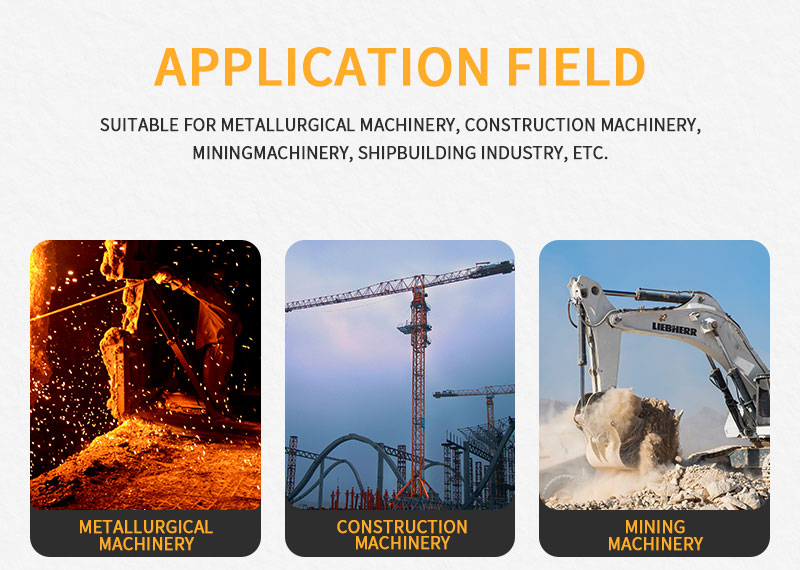
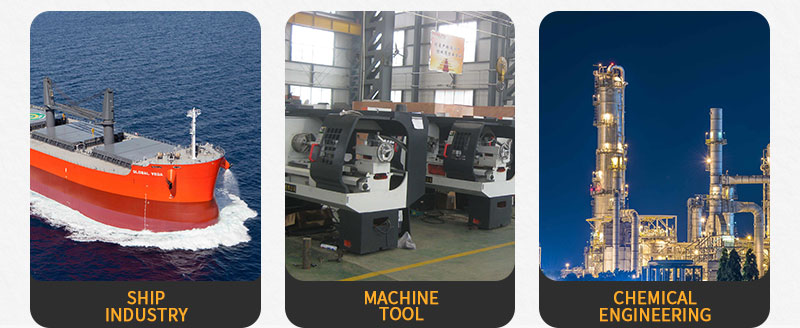