90R100DD1BC80L4S1EGBGBA262624 sauer danfoss pump
90R100DD1BC80L4S1EGBGBA262624 sauer danfoss pump
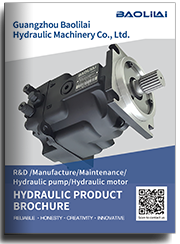
- Product Details
- Applicable Scene
Plunger pumps are widely recognized for their efficiency and reliability in fluid injection systems across various industries. These pumps are commonly used in applications requiring high pressure and precise fluid delivery, such as in the oil and gas, chemical processing, and water treatment sectors. To harness the full potential of plunger pumps, it is essential to follow best practices related to their selection, installation, operation, and maintenance. This article aims to outline these best practices to ensure optimal performance and longevity of plunger pumps in fluid injection systems.
90-R-100-DD-1-BC-80-L-4-S1-E-GB-GBA-26-26-24
90R100DD1BC80L4S1EGBGBA262624
One of the foremost considerations when implementing plunger pumps is the proper selection of the pump for specific applications. Factors such as fluid properties (viscosity, temperature, and corrosiveness), required flow rate, and operating pressure must be assessed. Utilizing a pump that matches these requirements can prevent operational inefficiencies and damage. Consulting with pump manufacturers or experienced engineers can facilitate choosing the right pump configuration, including plunger size, drive type, and sealing methods, to meet the demands of the application.
9623224C
Once the appropriate pump is selected, proper installation is crucial. An ideal installation minimizes stress on the pump and associated components. This includes ensuring that all piping is adequately supported and aligned, as misalignment can lead to premature wear and failures. It is also important to follow the manufacturer’s guidelines regarding any mounting specifications, such as orientation and vibration damping, which can impact the pump’s performance. Incorporating isolation valves and pressure gauges can further enhance control and monitoring during operation.
The operation of plunger pumps requires careful attention to parameters such as fluid temperature, pressure, and viscosity. Operating the pump within its specified limits is essential to avoid issues like cavitation, which can cause excessive wear and damage. Regular monitoring of these parameters and adjusting the pump settings as necessary ensures consistent performance and extends the lifespan of the equipment. In addition, periodic testing of the system for leaks, excessive noise, and irregular vibrations can help identify potential problems before they escalate.
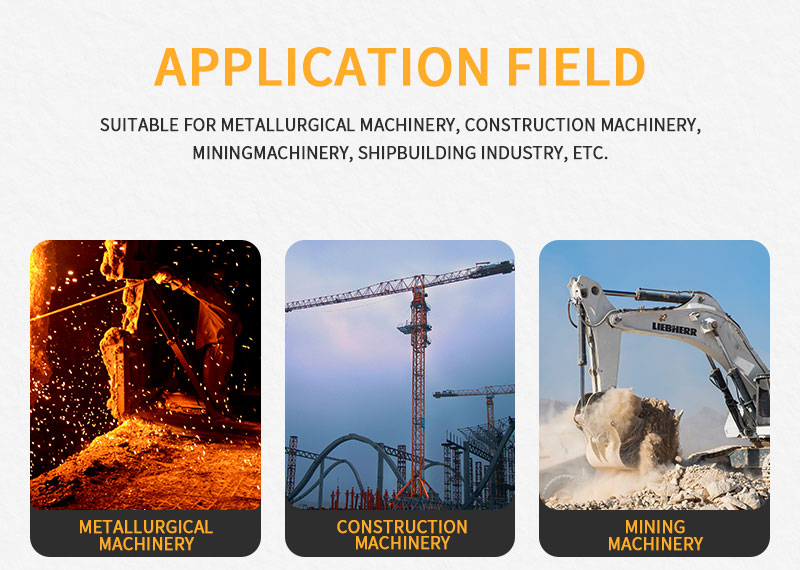
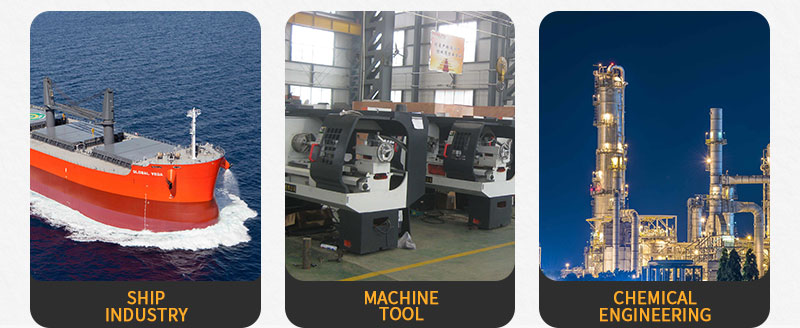