LRR030DLS2020NNN3C2RGA6NPLBNNNNNN piston pump
LRR030DLS2020NNN3C2RGA6NPLBNNNNNN piston pump
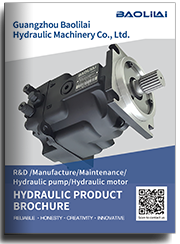
- Product Details
- Applicable Scene
Proper lubrication in aerospace piston pumps is crucial for maintaining their performance and longevity. These pumps operate under high-pressure and high-temperature conditions, making effective lubrication vital to prevent wear, reduce friction, and ensure reliable operation. Here are key strategies to ensure proper lubrication in aerospace piston pumps.
LR-R-030D-LS-20-20-NN-N-3-C2RG-A6N-PLB-NNN-NNN
LRR030DLS2020NNN3C2RGA6NPLBNNNNNN
Understanding Lubrication Requirements
7005032S
Each aerospace piston pump has specific lubrication requirements outlined by the manufacturer. These specifications include the type of lubricant, viscosity grade, and lubrication intervals. Aerospace engineers must thoroughly understand these requirements to select the appropriate lubricant and maintain optimal lubrication at all times.
Choosing the Right Lubricant
The proper lubricant enhances the performance of the piston pump. It is essential to select a lubricant that is compatible with the materials used in the pump, as well as resistant to high temperatures and oxidative degradation. Synthetic lubricants are often preferred in aerospace applications due to their superior properties, such as thermal stability, low volatility, and excellent lubrication characteristics.
Regular Lubrication Monitoring
Implementing a routine monitoring schedule for lubrication is essential. This can include regular checks of lubricant levels, viscosity, and contamination levels. Utilizing techniques such as spectrometric analysis or infrared analysis can help detect any degradation of the lubricant over time. Additionally, keeping detailed lubrication logs can help identify patterns and prevent potential issues before they arise.
Addressing Contamination Issues
Contamination is one of the most significant threats to effective lubrication. Dust, dirt, and other particles can compromise lubrication quality, leading to increased wear and reduced pump efficiency. To minimize contamination, it is important to implement proper sealing solutions and regular cleaning protocols. Additionally, using filtration systems can help maintain the cleanliness of the lubricant.
Implementing Timely Maintenance Practices
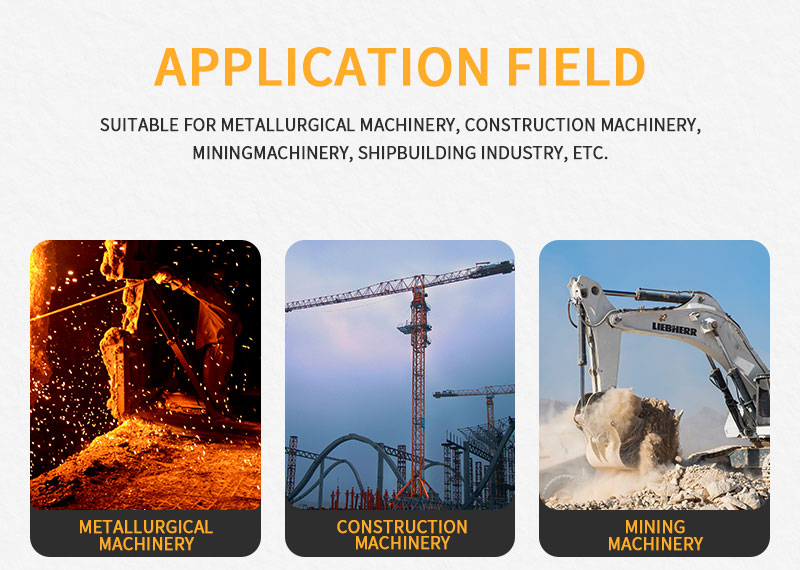
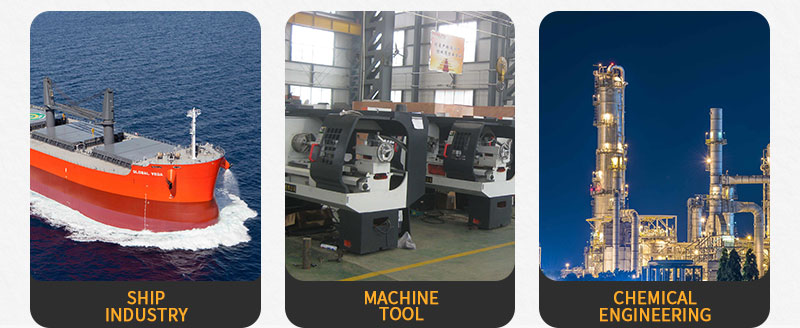