KRR045DLB2125NNN3C2NGA6NKNBNNNNNN danfoss pump
KRR045DLB2125NNN3C2NGA6NKNBNNNNNN danfoss pump
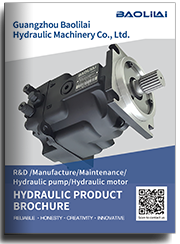
- Product Details
- Applicable Scene
As humanity pushes the boundaries of space exploration, the demand for advanced, reliable, and efficient systems becomes paramount. Among these systems, hydraulic oil pumps play a crucial role in ensuring the seamless operation of various spacecraft components, including landing gear, robotic arms, and maneuvering systems. The design of hydraulic oil pumps for advanced space exploration vehicles must address unique challenges posed by the harsh environment of space, including extreme temperatures, vacuum conditions, and radiation.
KR-R-045D-LB-21-25-NN-N-3-C2NG-A6N-KNB-NNN-NNN
KRR045DLB2125NNN3C2NGA6NKNBNNNNNN
One of the primary considerations in designing hydraulic oil pumps for space is the efficiency of fluid transfer. In a vacuum environment, minimizing leakage and ensuring the reliable flow of hydraulic fluid is essential. This necessitates advanced sealing technologies and precision engineering to maintain optimal pressure levels within the system. Utilizing materials that can endure temperature fluctuations and are resistant to outgassing is critical. For instance, specialized polymers and alloys might be employed to enhance the longevity and reliability of the seals used in these pumps.
7004229S
Another important factor is the weight-to-performance ratio. Spacecraft missions are often constrained by weight limits, necessitating the use of lightweight materials and designs that do not compromise performance. Employing computer-aided design (CAD) tools and finite element analysis (FEA) can help engineers optimize the structural design of hydraulic oil pumps, allowing for the reduction of unnecessary mass while maintaining strength and functionality. Additionally, integrating advanced manufacturing techniques, such as additive manufacturing or 3D printing, could result in components that are both lightweight and highly durable.
Temperature management is also a significant concern. Hydraulic oil pumps in space must operate efficiently within a wide temperature range, from the extreme cold of space to the heat generated during operations. This requires the selection of hydraulic fluids that possess stable viscosity characteristics over varied thermal conditions. Moreover, thermal insulation or active heating systems may be integrated into the pump design to maintain an optimal operating temperature.
Reliability and redundancy are essential in space exploration systems, as failures can have catastrophic consequences. Designing hydraulic oil pumps with built-in redundancy, such as dual-pump systems or backup power supplies, can help ensure that critical operations continue even in the event of a failure. Furthermore, rigorous testing and validation processes, including simulations of deep-space conditions, are vital to ensure that these components function as intended throughout the mission duration.
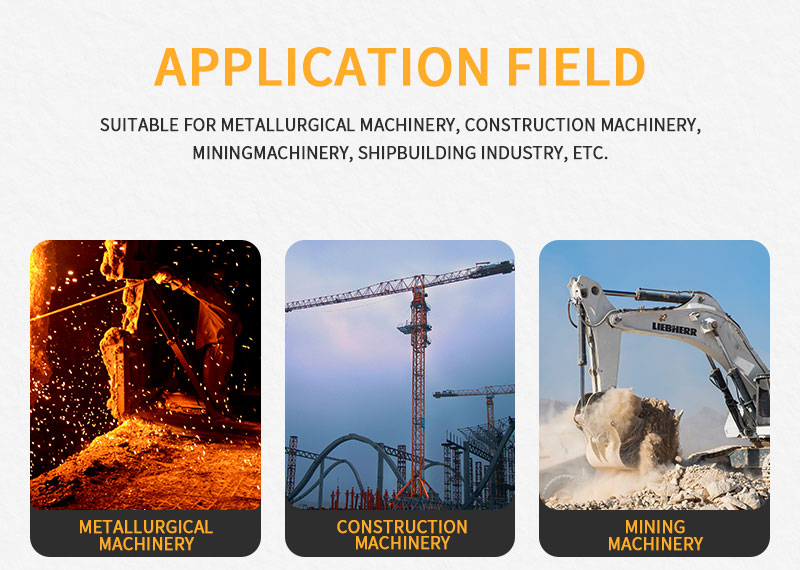
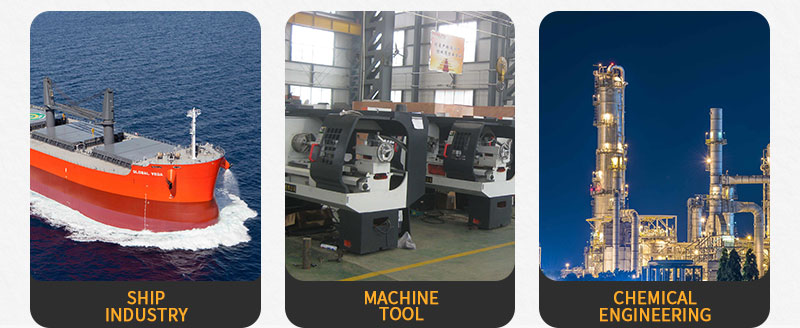