KRR045DLS1820NNN3C3NFA6NPLBNNNNNN sauer danfoss pump
KRR045DLS1820NNN3C3NFA6NPLBNNNNNN sauer danfoss pump
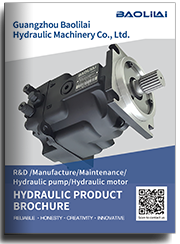
- Product Details
- Applicable Scene
Hydraulic oil pumps play a crucial role in various industrial applications, from manufacturing to construction. However, when these pumps operate in corrosive environments, such as chemical processing plants or offshore installations, the materials and design choices become critical to ensure longevity and reliability. This article delves into the key considerations and best practices for designing hydraulic oil pumps that can withstand corrosive conditions.
KR-R-045D-LS-18-20-NN-N-3-C3NF-A6N-PLB-NNN-NNN
KRR045DLS1820NNN3C3NFA6NPLBNNNNNN
One of the primary challenges in corrosive environments is material selection. Traditional metals like carbon steel can easily succumb to rust and deterioration when exposed to harsh chemicals, saltwater, or extreme pH levels. Therefore, engineers often opt for specialized materials such as stainless steel, bronze, or high-grade plastics. Stainless steel, particularly grades like 316, offers strong resistance to both corrosion and pitting, making it a popular choice. Additionally, coatings and linings, such as epoxy or fluoropolymer, can be applied to further protect metal components from chemical exposure.
83057852
Moreover, the design of seals and gaskets is critical in maintaining the integrity of hydraulic oil pumps in corrosive settings. Many standard seals can degrade quickly in hostile environments. Consequently, the use of chemical-resistant elastomers, like Viton or PTFE, is essential. These materials provide better sealing capabilities while enduring the chemicals present in the environment. Furthermore, the design should minimize the number of components that can harbor corrosive substances, thereby reducing the risk of leaks.
Another important aspect of designing hydraulic oil pumps for corrosive environments is ensuring effective maintenance access. Regular inspection and maintenance are vital to identify wear and potential failures early. Designing pumps with modular components allows for easier replacement of parts that may be more susceptible to corrosion, ultimately extending the pump’s lifespan.
In corrosive applications, pump hydraulic performance can also be affected. Engineers must consider how chemical reactions may change the viscosity and density of the fluid. Pumps should be designed with adjustable parameters to accommodate variations in fluid properties, ensuring optimal performance and efficiency under changing conditions.
Additionally, the environment in which the pump operates must be carefully analyzed. Factors such as temperature, humidity, and the presence of specific chemicals can greatly influence the chosen design and materials. For instance, high temperatures may necessitate the use of thermal-resistant materials, while elevated humidity levels could require additional protective measures to prevent galvanic corrosion.
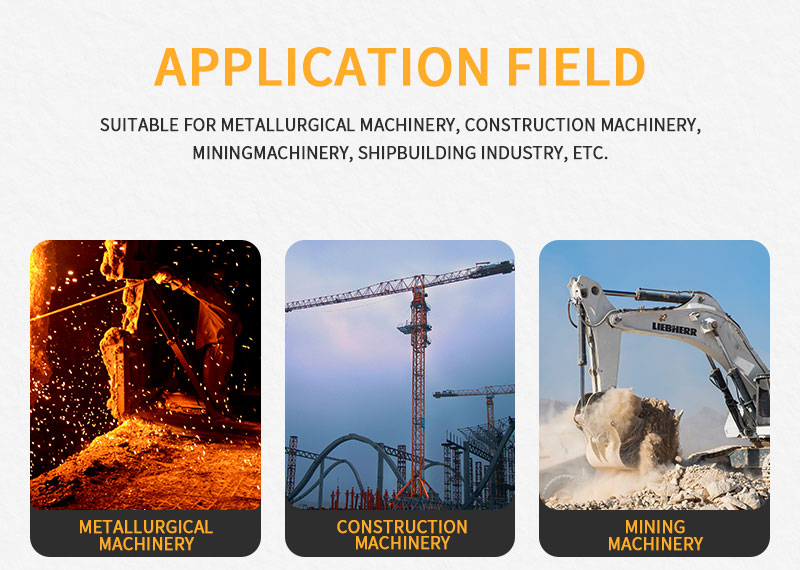
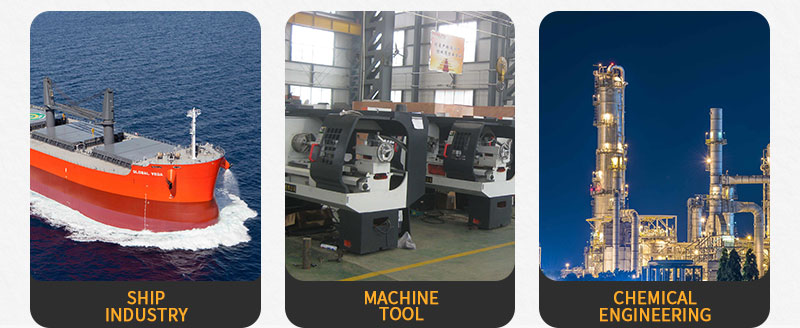