KRR045DLS2114NNN3C2NKA6NKNBNNNNNN sauer danfoss pump
KRR045DLS2114NNN3C2NKA6NKNBNNNNNN sauer danfoss pump
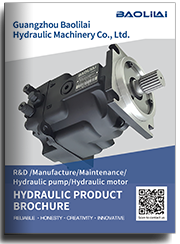
- Product Details
- Applicable Scene
Hydraulic oil pumps play a vital role in the operation of fluid power systems used in injection molding and casting processes. These applications require precise control and high efficiency to ensure product quality and reliability. In this article, we will explore the design considerations for hydraulic oil pumps used in these contexts, emphasizing their importance in achieving optimal performance.
KR-R-045D-LS-21-14-NN-N-3-C2NK-A6N-KNB-NNN-NNN
KRR045DLS2114NNN3C2NKA6NKNBNNNNNN
The primary function of hydraulic oil pumps in injection molding and casting is to provide the necessary hydraulic pressure that drives actuators, thus enabling the movement of molds and other components within the machinery. The design of these pumps must account for various factors, including flow rate, pressure requirements, system compatibility, and energy efficiency.
83053636
One of the critical aspects of pump design is the selection of the appropriate pump type. There are several types of hydraulic pumps, including gear pumps, piston pumps, and vane pumps. Gear pumps are often favored for their simplicity and reliability, making them suitable for applications with constant flow requirements. Piston pumps, on the other hand, can handle high-pressure applications and offer better volumetric efficiency, making them ideal for injection molding processes where precise control is necessary. Vane pumps provide a balance between efficiency and ease of maintenance, making them suitable for a variety of applications.
Flow rate and pressure are essential parameters in the design of hydraulic oil pumps. The flow rate must match the operational needs of the injection molding or casting process to ensure smooth and consistent operation. Additionally, the pressure levels generated by the pump must be within the specified ranges to prevent damage to the machinery and ensure safety. Engineers must conduct thorough calculations and simulations to determine the optimal pump specifications for a given application.
Material selection is another important consideration in the design process. Hydraulic pumps are exposed to high pressures and potentially corrosive hydraulic fluids, making it crucial to choose materials that can withstand these conditions without degrading. Common materials used include various steels, aluminum alloys, and specialized coatings that enhance wear resistance.
Another key factor in the design of hydraulic oil pumps is the need for energy efficiency. As environmental concerns and operational costs become increasingly critical, manufacturers are looking for ways to reduce energy consumption without compromising performance. Innovative designs, such as variable displacement pumps and electronic controls, can help optimize energy use by adjusting flow and pressure in real-time based on the machine’s requirements.
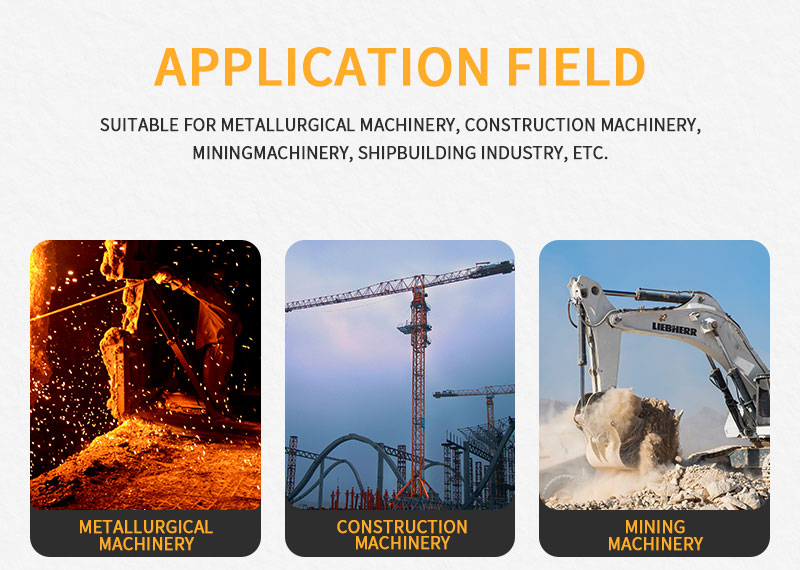
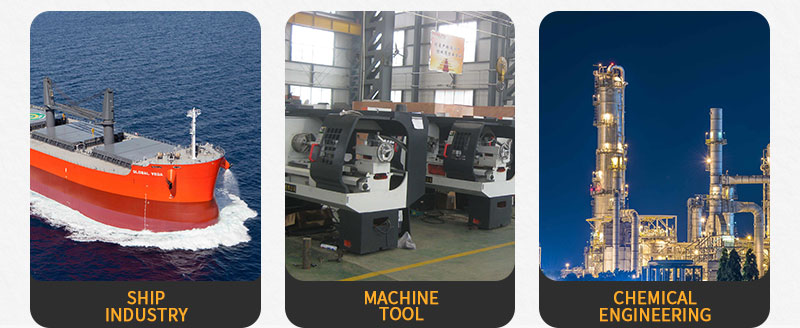