KRR045DPC10NNNNN3C2NRA6NAAANNNNNN hydraulic pump
KRR045DPC10NNNNN3C2NRA6NAAANNNNNN hydraulic pump
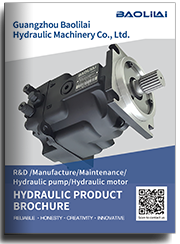
- Product Details
- Applicable Scene
The logistics industry relies heavily on efficient material handling systems to ensure smooth operations. Among the various systems in place, hydraulic lifts and elevators play a pivotal role in moving goods vertically within warehouses and distribution centers. The design of hydraulic oil pumps for these applications is crucial to enhance their performance and reliability. This article discusses the key considerations and design elements involved in creating hydraulic oil pumps specifically tailored for hydraulic lifts and elevators used in logistics.
KR-R-045D-PC-10-NN-NN-N-3-C2NR-A6N-AAA-NNN-NNN
KRR045DPC10NNNNN3C2NRA6NAAANNNNNN
One of the foremost considerations in designing hydraulic oil pumps is the specific requirements of the hydraulic lifts and elevators. These systems must be able to handle varying loads and operate under different conditions. The hydraulic pump must deliver precise flow rates and pressure to ensure smooth and safe movement of goods. Therefore, it is essential to have a deep understanding of the operational parameters, including maximum load capacity, speed of operation, and the type of hydraulic fluid used.
83015917
Another critical factor in the design process is the choice of pump type. There are several different types of hydraulic pumps, including gear pumps, vane pumps, and piston pumps. Each type has its advantages and disadvantages depending on the application. For hydraulic lifts and elevators, gear pumps are often favored for their simplicity, efficiency, and reliability. However, piston pumps may be used for applications requiring higher pressure and efficiency.
Efficiency is a key concern in the logistics sector due to competitive pressure and the need to minimize operational costs. As such, designers must focus on creating hydraulic oil pumps that provide high efficiency while maintaining low energy consumption. Hydraulic systems that waste energy during operation can significantly affect overall system performance, leading to increased operational costs. Therefore, selecting high-quality components and optimizing the design for reduced turbulence and friction losses are vital steps in achieving efficient pump performance.
Reliability and durability are also paramount in the design of hydraulic oil pumps. The logistics environment is often demanding, with pumps subjected to heavy use and potential exposure to contaminants. Therefore, materials used in the construction of the pump must be resistant to wear and corrosion. Additionally, incorporating features such as robust seals and filtration systems can enhance the longevity of the pumps and reduce maintenance requirements.
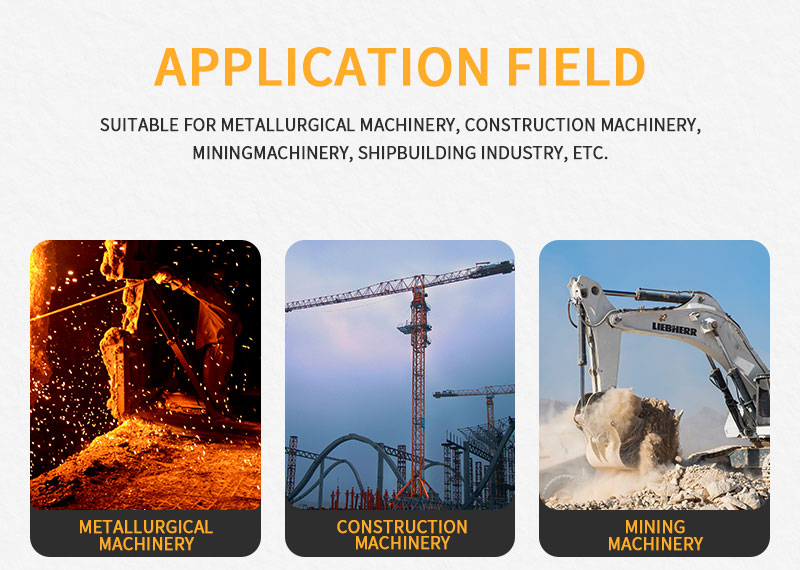
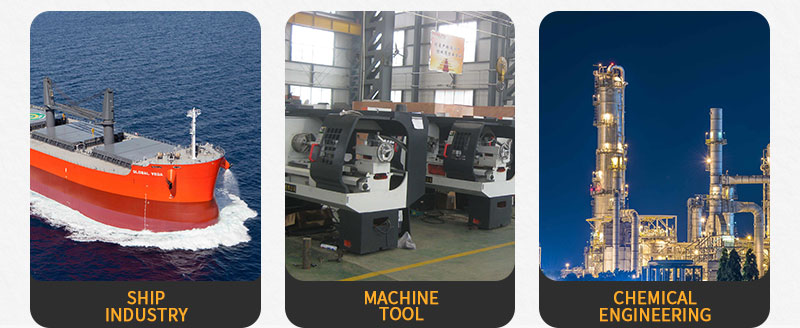