90L130MA1NN80P3F1F09GBA454520 sauer danfoss pump
90L130MA1NN80P3F1F09GBA454520 sauer danfoss pump
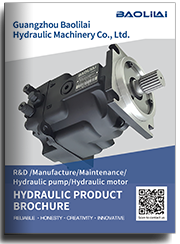
- Product Details
- Applicable Scene
Hydraulic pumps are critical components in numerous industrial applications, often responsible for powering machinery and equipment by converting mechanical energy into hydraulic energy. In low-flow, high-pressure environments, the risk of hydraulic pump failures can significantly increase, leading to downtime and costly repairs. Understanding the root causes of these failures and implementing preventive measures is essential for maintaining system efficiency and reliability.
90-L-130-MA-1-NN-80-P-3-F1-F-09-GBA-45-45-20
90L130MA1NN80P3F1F09GBA454520
One of the primary causes of hydraulic pump failure in high-pressure applications is cavitation. This phenomenon occurs when the pressure within the pump drops below the vapor pressure of the hydraulic fluid, leading to the formation of vapor bubbles. When these bubbles collapse, they create shock waves that can cause severe damage to the pump’s internal components. To prevent cavitation, always ensure that the hydraulic reservoir is adequately filled and that there is sufficient fluid supply to maintain proper suction pressure. Additionally, using a pump with an appropriate pressure rating and flow characteristics can also mitigate this risk.
513750
Another critical factor is the selection of suitable hydraulic fluid. In low-flow scenarios, the temperature of the hydraulic fluid may rise due to insufficient cooling, leading to a decrease in viscosity. A fluid with the correct viscosity and thermal stability is vital for efficient pump operation. Regularly monitoring fluid levels and temperatures, as well as replacing fluids that have degraded, will help maintain optimal performance.
Contamination is a silent killer of hydraulic systems. Particulate matter, water, and other contaminants can lead to increased wear and tear on pump components, ultimately causing failure. Implementing a robust filtration system is crucial for removing impurities from the hydraulic fluid. Regular maintenance schedules that include fluid sampling and analysis can help identify contamination issues before they escalate.
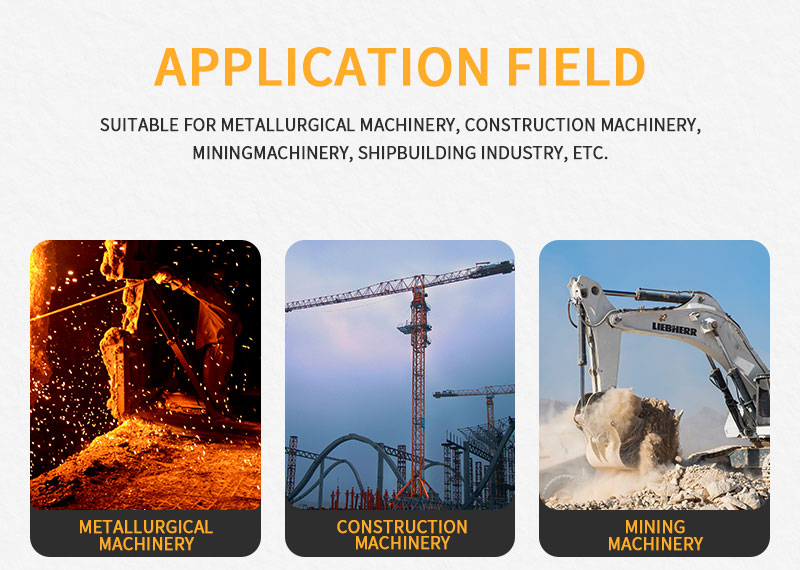
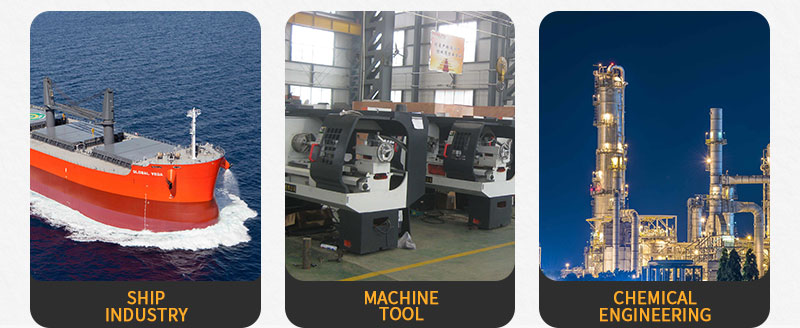