90L130KP1NN80L3F1F03GBA353520 sauer danfoss pump
90L130KP1NN80L3F1F03GBA353520 sauer danfoss pump
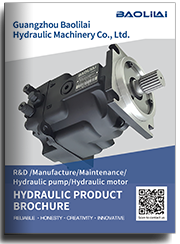
- Product Details
- Applicable Scene
In various industrial applications, hydraulic pumps play a critical role in ensuring the precision and efficiency of fluid circulation. Optimizing their operation not only enhances performance but also extends the lifespan of the equipment and minimizes operational costs. Here are some key strategies to achieve optimal hydraulic pump operation for precision fluid circulation.
90-L-130-KP-1-NN-80-L-3-F1-F-03-GBA-35-35-20
90L130KP1NN80L3F1F03GBA353520
Firstly, proper selection of the hydraulic pump is essential. Different applications require different types of pumps based on factors such as viscosity of the fluid, flow rate, and pressure requirements. Understanding the specific operational needs and characteristics of the fluid being processed can guide you in choosing the most suitable pump.
83022430
Next, regular maintenance is crucial for optimal pump performance. This includes routine inspections and timely replacement of worn-out parts such as seals and bearings. Implementing a preventative maintenance schedule can help identify potential issues before they lead to costly downtimes or pump failures. Additionally, monitoring fluid quality is important; dirty or contaminated fluids can lead to increased wear and reduced efficiency.
Calibration of the pump system is another vital factor. Ensuring that the system is calibrated correctly, based on the desired flow rates and pressure readings, can significantly improve performance. Utilize flow meters and pressure gauges to monitor real-time performance and make necessary adjustments to the system.
Managing hydraulic fluid temperature is also paramount. Excessive heat can cause the fluid to break down, compromising its ability to lubricate and transmit power effectively. Incorporating cooling systems or heat exchangers can help maintain optimal fluid temperatures and improve overall system efficiency.
Moreover, minimizing turbulence and cavitation can enhance hydraulic pump performance. Smooth, gradual bends in piping and appropriate sizing of hoses can reduce friction and flow disruptions, thus improving the flow characteristics. Cavitation occurs when vapor bubbles form in the fluid due to pressure drops, leading to potential damage and inefficiencies. Ensuring that the pump operates within its specified NPSH (Net Positive Suction Head) can help prevent cavitation.
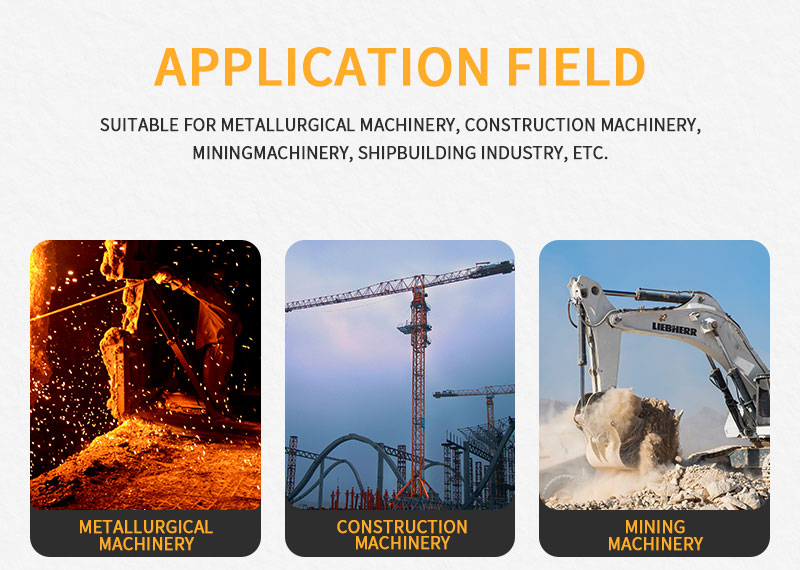
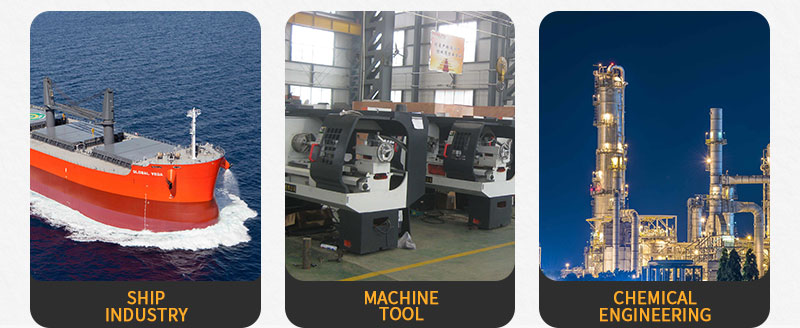